This tutorial is about the assembly of the Mid Stomach parts.
Beware that these parts will certainly be obsolete and temporary once the legs are done. I post them anyway because many builders asked for them. There is pictures missing in this tutorial, I lost them with a hard drive…
Download STL files from the Gallery
Before printing all the parts you should print the CALIBRATOR, to check if your parts will fit together. If you have a very hard time putting those parts together, adjusting the horizontal expansion setting of your slicer software can solve that, this setting can vary depending of your slicer and printer but users report to set it at -0.15 is a great place to start.
An infill of 30%, wall thickness 2.5mm, best with no raft, no support(unless specified), use a brim for big parts to avoid warping.
You will need to print all these parts:
- 1x BotBackLeft
- 1x BotBackRigt
- 1x BotCapLeft
- 1x BotCapRight
- 1x BotFrontLeft
- 1x BotFrontRigt
- 1x HipCoverFront
- 1x HipCoverLeft
- 1x HipCoverRight
- 1x MidPotHolder
- 2x MidWormRight
You will need 2 servos HS-805bb which needs to be hacked. Both motor servos will be using only one servo board and one potentiometer, this way both motors will be synchronised when rotating. This will be explained in the tuto.
You will need between 65 to 70 ball bearings. You can use steel or BB Gun balls. They should be 6mm diameter.
I tried to use Vigor VSD-11AYMB servos and made some files files adapted for it. Unfortunately these servos aren’t good because they jitter sometimes. Another annoying factor is that they won’t “detach” properly through software.
Step1: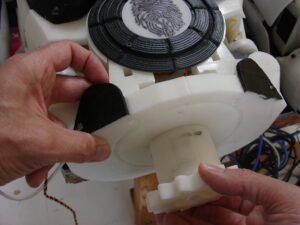
Check that StomGearV2.stl fits correctly into the Top Stomach parts.
Also make sure that StoGearAttachV1.stl seats well on the bottom surface of the Top Stomach parts. For more info check the tutorial on TopStomach.
Step2:
Assemble together BotBackLeftV1.stl , BotBackRigtV1.stl , BotFrontLeftV1.stl , BotFrontRigtV1.stl.
It is best to glue them together laying on a flat surface.
There is also the option to mount bolts for those of you that prefer.
Make sure the flat surface is as flat as possible.
If the surface is too uneven, glue a sheet of sand paper with double side tape on a flat board, and sand down your assembly until you are satisfied.
Smooth up the surface where the ball bearing will take place. I personnaly used Acetone because my parts are printed in ABS.
Cut off the pre-support on the HipCoverFrontV1.stl.
Mount with 3mm screws the HipCoverFrontV1.stl to your assembly. In my case I sprayed the black parts with car aerosol mat finish paint using masking tape.
Mount the two MidWormRightV1.stl to the servo horns with screws. Fit the servos on your assembly using wood screws. The connection wires of the servos will be detailed later in step3.
At this stage it is a good idea to make sure StomGear fits well through your assembly.
Put a good load of greaseon the wormgears and in the passthrough hole for StomGear.
Check the potentiometer hole on StomGear and position it as shown.
Fit in StomGear.
Make it go all the way through your assembly.
Step3:
Hacking the servos
You will need to remove the potentiometer from your servos as described in this tutorial. Remember that the Vigor VSD-11AYMB servos are slightly different than the Hitec805BB. The below tuto explains for Hitec805BB.
The two servo need to be hacked for continous rotation.
One of the two servo will be controlled by the other so you have to remove the board and potentiometer of this servo (keep it preciously for spare part as if one day you burn a 805B servo controller board).
Three welding to remove to detach the servo controler board and the square potentiometer
Weld two Wires directly on the motor, dot red point for positive (I suppose).
and cut as usual the small piece that block the full rotation of the servo motors.
Set the blue cable on the positive side of the motor (red dot)
On the other motor, set the brown cable on the positive side of the motor.(red dot)
Make sure you have reversed the color cable to the motor polarity. This way one motor will turn one way and the other will turn the other way.
Step4:
Missing pictures: Assemble together on a flat surface BotCapLeftV1.stl and BotCapRightV1.stl . Use Acetone if ABS prints or Epoxy if PLA prints.
Mount the potentiometer on MidPotHolderV1.stl, respecting the small metal positioner. Glue MidPotHolderV1.stl to the BotCap.
Set the BotCap assembly on the main assembly.
Use 4mm screws to fix BotCap to main assembly.
Mount TStoLowLeftV1.stl and TStoLowRightV1.stl to your main assembly.
Using a clamp to press fit will ease the job.
Add 4mm screws, making sure the screw head is well sinking into the part. Otherwise it will restrain rotation between TopStomach and MidStomach.
Add screws on the sides as well.
Step5:
Add a good load of grease on your assembly flat bed.
Add some 6mm ball bearings, I used BB Gun balls which do the job quite well until now.
Apply grease on the flat bed of TopStomach as well.
Fit in the StomGear to assemble TopStomach and MidStomach together.
Use 4 screws of 4mm to fix StomGearV2.stl to StoGearAttachV1.stl as already seen in the tutorial of Top Stomach
Adjust the bolts to make sure TopStomach and MidStomach are well tight. But don’t overtight because we want to keep these parts some freedom for rotation.
Time now to run some script test to see if all is set in order.
Hi Gael,
This is awesome! Thank you! From the videos it looks like this set up works really well.
I am slowly working my way down the torso to the stomach parts and am starting to review this as I get closer.
Two questions:
1. Are two servos necessary to make the stomach rotate? Does one of the big servos not generate enough torque to move everything?
2. The slave servo is an interesting solution. I’m guessing that you could not just reverse the worm gear because the stomgear is angled. Correct?
I truly appreciate all the work you put into this. Thank you!
Scott
I’m glad you enjoy the build up process!
I would guess just one servo might be enough, but I haven’t tested, so it’s up to your own choice.
I had tried a version with a reversed wormgear with a no angled stomgear, but since stomgear turns in one direction it necessarily implies to reverse the direction of the opposite wormgear. Therefore polarity on the slave servo has to be reversed.
Im a bit confused.
Can i use HS805BB as servos or does it has to be Vigor VSD-11AYMB ?
For the Midstomach side rotations, you need two HS805BB.
For the LowStomach rotations you need two Vigor servos.
Do rotacji LowStomach użyłem dwa serwa HS805BB tylko przeprojektowałem MidWormRightV1 oraz StomGearV2 jeśli ktoś poturbuje mogę przesłać pliki
Is there a MidPotHolder for a square potentiometer? I can’t find any mention of it on forum or thingiverse.
Hi Gael,
Do you mean to install the VSD-11AYMB servo board in the HS805bb structure in the Step3? I see the VSD servo motor is the 50kg spec, can I use other models of the 50kg steering servo plate?
I use this servos, and she works well.
CYS 8503 30 kg Digital Metal Gear Servo
Thanks for your information about this servo.
on the use of the cys 8503 – do you have a design for the coupling plate? the servo head seems quite far away from the worm gear? How did you bridge the gap? Its very tight between the worm gear and the casing / mount? Would be intrested in seeing a picture of how you coupled it.
Also the cys 8503 is shorter than the HB-805bb so will have to alter the mount too for it to be secure.
Alan
Bonjour a tous
Petit soucis avec le potentiomètre du mi-torse
Quand je dis a Inmoov “prend la bouteille” le cerveau tourne,
Quand je dis “relax” il tourne du même sens, il ne revient pas au centre.
Est-ce-que ça peut venir des fils du potentiomètre ? merci
Hello,
C’est plutôt étrange.
Il faudrait tester sans utiliser les gestuelles, ni START_INMOOV.bat.
Il faudrait juste utiliser SERVO_CALIBRATION.bat et voir comment le servo master se comporte en utilisant le slider. (Attention, il faut reporter vos mappings de vos config manuellement , une fois le service servo démarré, afin d’éviter des surprises de mouvement brusque)
Si le problème continue, débrancher le servo slave, afin de voir si ce n’est pas lui qui serait branché avec une polarité qui contredirait le servo master.
Bonjour Gael
Merci
J’avais inversé les deux fils du potentiomètre c’est bon ça fonctionne j’ai aussi commandé la deuxième nervo board
Ah bah tout simplement…
La commande est préparée, si la poste n’est pas en grève demain, elle partira dans votre direction.
Bonjour Gael Pourquoi le reset et à 95 au lieu de 90
Bonsoir,
Un peu de précision car je ne sais pas de quoi vous parlez.
Le reset de quoi?
bonjour gael
Je ouvre myrobotlab je vais sur toi estomac les cerveaux ne sont pas à 90 au relax mets à 95 j’espère que j’arrive à m’expliquer merci
Je prends un exemple quand je dis au robot prends la bouteille le robot se penche normalement à 60 mais là il est à 90
quand je lui dis au relaxe il doit être normalement à 90 il se met à 95
Merci excusez-moi pour les fautes j’écris avec une dictée vocale
Bonjour,

La position “relax” ne remets pas les servos en position “rest”. Il prends une pose qui doit lui donner un air “cool”. Si on edite la gestuelle python “relax.py”, on peut voir:
i01.moveTorso(95,90,90)
Pour que tout les servos se re-positionnent en “rest”, il faut dire “METS TOI AU REPOS”.
Ok Gael merci beaucoup je vais tester ça et encore merci si tu viens un jour dans le var Fréjus dites-moi le je viendrai vous voir merci
Bonsoir Gael
J’ai testé j’ai dit à
Inmoov mets-toi au repos le curseur s’est mis à 90 mets le robot c’est pas chez du côté droit
Pour moi c’est peut-être un mauvais réglage du potentiomètre merci
Oui c’est un mauvais positionnement du potentiomètre.
Bonsoir Gael
Merci pour ta réponse Gael et pour te dire aussi que j’ai bien reçu mon colis merci
Parfait, bonne continuation!
Hola Gael, saludos desde Perú. Voy a iniciar el estomago medio, las partes estan vigentes o cambiaron al terminar las patas. (Hay un warning al inicio del tutorial, tal vez del 2016). Gracias y Feliz Año
Hell and Happy New Year!
Maybe when the motorised legs will be finished , you might need to print another model for the mid and low stomach. But there is so much work still on the motorised legs that I suggest you print the parts anyway for now.
Hola Gael, quizás no me explique bien. Al inicio del tutorial del estomago medio, anunciaste que cuando termines las patas (lo que ya sucedió), las partes del estomago medio estarían desactualizadas u obsoletas. Mi pregunta es si hubo variaciones?, o ya se actualizó?, o no hubo cambios?
Es decir puedo usar las partes publicadas, para el estomago medio o hay variaciones ¿? Saludos y gracias por su respuesta.
Hello,
Yes you can use the published parts for the “non” motorized legs.