Building the bicep of InMoov
I have tried to make this as simple as I could, and I hope you will find answers to your questions here. Once you have printed the parts you can start the job. On these pictures I was assembling the left arm so take that in consideration if you are building the right arm.
Download STL from the Gallery
Before printing all the parts you should print the CALIBRATOR, to check if your parts will fit together. If you have a very hard time putting those parts together, adjusting the horizontal expansion setting of your slicer software can solve that, this setting can vary depending of your slicer and printer but users report to set it at -0.15 is a great place to start.
An infill of 30%, wall thickness 2.5mm, best with no raft, no support, use a brim for big parts to avoid warping.
Here is the list of parts and the number of prints needed for 1 right bicep:
- 1x GearHolder
- 2x HighArmSide
- 1x Pistonanticlock
- 1x Pistonbaseanti
- 1x RotGear
- 1x RotMit
- 2x PivPotentio (round or square)
- 1x RotTit
- 1x RotWorm
- 1x Rotcenter
- 1x armtopcover1
- 1x armtopcover2
- 1x armtopcover3
- 1x elbowshaftgear
- 1x gearpotentio
- 2x lowarmside
- 2x reinforcer
- 1x servobase
- 1x servoholder
- 1x spacer
Here is the list of parts and the number of prints needed for 1 left bicep:
- 1x GearHolder
- 2x HighArmSide
- 1x Pistonanticlock
- 1x Pistonbaseanti
- 1x RotGear
- 1x RotMit
- 2x PivPotentio (round or square)
- 1x LeftRotTit
- 1x RotWorm
- 1x LeftRotcenter
- 1x armtopcover1
- 1x armtopcover2
- 1x armtopcover3
- 1x elbowshaftgear
- 1x gearpotentio
- 2x lowarmside
- 2x reinforcer
- 1x servobase
- 1x servoholder
- 1x spacer
STEP1:
What we want to do in this first tuto is to extract the potentiometer of the 2 servos and adding by welding, extra cable length:
We will start by opening the Hitec HS-805BB servo by unscrewing all the screws at the bottom. It comes apart in three sections. Make sure to work in a clean place, you don’t want to lose anything and spoil the grease it contains. Once the top is removed, note or take a picture of each gears placement, check well there are two looking almost alike (shown on picture).
Remove the bearing and it’s rings(note the order). It can be a little hard to remove it, I used a small screw driver placed under the bearing.
Now we want to remove the pcb card and it’s motor, on some servos it just came easy, but there is a bit of glue around the motor, so you can push the motor down by pressing the little metal gear placed at the tip of my screw driver.
Here is another solution posted by an InMoov builder, if you can’t open up your servo the way I did it, of course if you have a solder pump, it will be even easier:
Or this video:
Or you can also watch these videos posted by a InMoov builder:
Here is another set of videos, in which the technique involved is to remove the solder on the three motor connections, leaving the motor in place instead of romoving it:
A PDF for to extract the potentiometer on a JX-PDI2060MG servo:
Aaah, it came out, unscrew the potentiometer, for to release it out see next picture.
help yourself again with your small screwdriver placed under the big gear.
Remove the plastic washer(we won’t need it anymore, but keep it you never know…)
This is a bit tough, cut the “stopper” with a knife or pliers, BUT DON’T DAMAGE THE GEAR.
Remount all the gears back in there original place. Arrange with your knife a bigger opening for the extra length cables. When unwelding the cables from the board and the potentiometer note the colors. (I didn’t with my first servo, answered the phone for ten minutes and when I went back for welding I couldn’ remember the colors… Caused to damage the servo permanently, 30euros in the trash, Aaargh)
Before welding the potentiometer of the low part of bicep, run your cables in the gap of “servoholderV1”.
Important note: do not de-solder the potentiometer wires from the PCB of the servo, just cut them and solder the extra length you need. Some builders have reported having none working servos after soldering directly on the PCB controller. Some components might be very delicate to temperature.
For the low part servo of the bicep, your cables should be welded in the same color order as when you opened the servo. Your cables should be about 25/30 cm long. Now we are set for to assemble the parts.
Here is another solution (by Wayne Kinne) if you can’t open up your servo the way I did it, of course if you have a solder pomp, it will be even easier:
You can also watch these videos posted by a InMoov builder (byKaibab):
Here is another set of videos (by Yann Huguenin), in which the technique involved is to remove the solder on the three motor connections, leaving the motor in place instead of romoving it:
STEP2:
This picture is to show you what is the angle position of “rotgearV1” compared to “rotmitV1”. Check the little rectangle hole.
So keeping the same rotation angle, mount “rotmitV1” to “rotgearV1”. (Don’t refer to this picture for the angle, parts you’ve downloaded aren’t the same anymore)
I used clamps to make sure there wouldn’t backlash between all three parts during screwing them. Make sure your screws don’t come out behind, or recut them. (Don’t refer to this picture for the angle, parts you’ve downloaded aren’t the same anymore)
Attach one servo to “rotcenterV1”. For to do so: mount but don’t tight fit the white actuator wheel.

Once the servo is attached, you can tight the screw.
Mount “rotwormV4” to the actuator with 4 little screws, make sure they don’t come out behind the actuator, otherwise you have to cut them. Mount “rotgearV2” to “rotcenterV2”, it should turn easily but with no backlash. I made it operate a few turns by plugging the servo on the Arduino. Then I cleaned up the dust created by the parts. Before closing the case with “rotTitV1”, use a good amount of grease, every where on the gears.
If you are building the left ROTATE arm, your cables should be welded in the same color order as when you opened the servo.
If you are building the right ROTATE arm, your cables should be welded in the opposite color order as when you opened the servo.
Mount the potentiometer to “rotpotentioV2” but make sure to place the little metal plate from the potentiometer in the gap designed in “rotpotentioV2”. Use some little spare screws from your small servos.
PS: “rotmitV2 was not supposed to be standing on the left on three above pictures, since you already have mounted it…
Ease “pistonanticlockV1” in to “pistonbaseV1”. I have reinforced “pistonanticlockV1” on the inside with a metal rod. But you can use it like this, it should hold. I broke a few of them during my tests, and was glad they could break instead of something else.
Assemble “higharmV1” to “rotmitV1″”, use pliers , with ABS it just fit perfectly, I felt like playing with Lego’s. Make sure you have the same position then on the picture.
Add “pistonbaseV1” and “spacerV1”. Attach the potentiometer, again make sure to place the little metal plate from the potentiometer in the gap designed.
Assemble the rest of “higharmV1” and “lowarmV1”. Later, after your tests, you will have to glue those parts.
Attach the servo in the “servoholderV1”.
Run the cables as shown.
Tuck down the cable along the frame as shown on this picture, I used aluminium tape, this will avoid pinching the cable during actuations. Do the same on the other side with the potentiometer wires.
Attach the “servobaseV1”, and “pistonanticlockV1” to the actuator.
Turn in “pistonanticlockV1” in to “pistonbaseV1”. Adding grease is a good idea.
So I assume here you already have glued “elbowshaftgearV1” to “robcap3V1”. So you also have attached the forarm to the bicep. Good.
Here comes the part the most difficult for me to explain. Now lean down “servobase” and attache it to the forarm.
You should KEEP a gap at it’s base, this is going to be your 0° degree position. Fix or mark the whole arm in this position, it is important not to lose it during the next steps.
Unmount the servo gun. Plug your servo to the Arduino board, and run a sketch to get the 0° position of your servo, it will rotate continuously. Now turn by hand the potentiometer until the servo stops turning. This is your 0° degree position.
Mount the “potentiogearV1” on the potentiometer, making sure the arm and the potentiometer don’t move.
Clip in the “gearholderV1”. There should not be backlash between the two gears. Keep the servo gun unmounted and make a test with your Arduino like previously to 0°degree. You can move the arm slowly by hand to closed position and open position to check everything is okay. Remount the servo gun.
Big moment now. Rerun the test to 0°degree. The arm should open keeping the gap previously seen at the base. If not it will break the “pistonanticlockV1”.
Make another test from 0°degree to 60°degree. Check the space left between “pistonanticlockV1” and “pistonbaseV1”. My arm can go up to 90°, but be carefull that all depends on the gap you have set. So try 10° by 10°degrees. Remember when writing your sketchs to never go further then the best result you got.
Now you can make a test with the servo attached to “rotcenterV1” going to 90°, that will be the “rest” position of the arm when it will be attached to the coming shoulder.
Add the covers on the bicep to reinforce the structure.
There is no support to remove on these parts. But you need to cut the tiny connectors, between the parts, to separate them. A cutter blade works with ABS, you might need to use a knife with teeth, if printed in PLA.
The covers are glued together to match the bicep like on this picture:
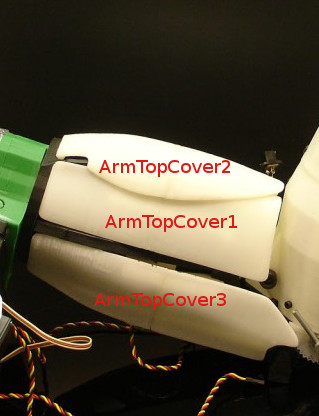
Normally you should be all set. Hope this helped because it took me a lot of time to do this tuto 🙂