All right let see how we’re going to proceed. In this tuto we are going to build the shoulder and torso simulteanously. I would have rathered do it separatly, but my pictures were already done this way, and I’m not going to take the robot apart for to make new pictures.
Download STL files from the Gallery, Shoulder and Torso
Before printing all the parts you should print the CALIBRATOR, to check if your parts will fit together. If you have a very hard time putting those parts together, adjusting the horizontal expansion setting of your slicer software can solve that, this setting can vary depending of your slicer and printer but users report to set it at -0.15 is a great place to start.
An infill of 30%, wall thickness 2.5mm, best with no raft, no support(unless specified), use a brim for big parts to avoid warping.
Here is the list of parts and the number of prints needed for the torso:
- 2x: KinectSideHolder
- 2x: KinectSideBack
- 1x: KinectMidFront
- 1x: KinectMidBack
- 2x: InterKinectSide
- 2x: InterKinectMid
- 2x: HomLowFront
- 2x: HomLowBack
- 2x: ChestLow
Here is the list of parts and the number of prints needed for 1 right shoulder:
- 1x ClaviBack
- 1x ClaviFront
- 1x PistonClavi (if you have a trouble fitting this part with pistonbase, you can decrease the X and Y size before printing of 0.1 or 0.2mm)
- 1x Pistonbase
- 2x PivConnector
- 1x PivGear
- 1x PivMit (add support)
- 2x PivPotentioRound or PivPotentioSquare
- 1x PivPotholder
- 1x PivTit (add support)
- 1x PivWorm
- 1x Pivcenter
- 1x servoHolster (add support)
- 1x servoholder
- 1x shoulderconnect
STEP1:
Follow the step1 in “Building the bicep of InMoov” for to extract the potentiometers of your servos.
Here is another solution posted by an InMoov builder (Wayne Kinne) if you can’t open up your servo the way I did it, of course if you have a solder pump, it will be even easier:
Or you can also watch these videos posted by a InMoov builder (by Kaibab):
Here is another set of videos (by Yann Huguenin), in which the technique involved is to remove the solder on the three motor connections, leaving the motor in place instead of removing it:
Or this video:
A PDF for to extract the potentiometer on a JX-PDI2060MG servo:
IMPORTANT: There is a difference though in the last part during re-welding the cables to the potentiometer depending if you build the right or left shoulder.

Weld the cables this way, if you are building the right shoulder. In this picture the blue replace the green or the black wire depending on your servos.

Weld the cables this way, if you are building the left shoulder. In this picture the blue replace the green or the black wire depending on your servos.
This will allow your servo to turn the opposite way making your initial 0 position becoming your 180 position. And your initial 180 position become your 0 position. I hope you get the idea. This will be done on both servos used in each shoulder. Now let start the assembly.
STEP2:
If you plan on building both shoulders you should repeat most of the following steps explained bellow for the other side of the body.
Remove the pre-built support under “PistonBase”
Make sure “PistonClavi” can run freely inside. If your prints are a bit too tight you can ease it with grease. I had to fine tune my printer for those parts to get the right setting.
Assemble together with your favorite pliers, “PistoBase”, “ClaviBack” and “HomPlatback+”.
If you are building in PLA, you can use a hot air gun to get parts warmed up to get them to fit easier, it avoids braking parts.
Make sure that “PistoBase” can rotate smoothly.
Add “HomPlatback-“to “HomPlatback+”
Here you can see my favorit pliers in action.
Add “ThroatHole” to “HomPlatback-“to “HomPlatback+”
“ThroatHole” has been modified since this picture.
Time to assemble the front. Mount together “Sternum” to “ClaviFront”.
Sorry this picture shows the first version I made but it’s pretty close, check the next picture.
This is the shape you will obtain with the last version and the last “ThroatHole” in the back.
Mount together the two “ThroatLower” and “ServoHolster”.
This servo, set in the middle of the torso, is for to move the head up and down and can be added later if you wish, but the holster should be set already in place.
Mount this assembly to the back assembly. Check on the picture the plots and the position of the servo. Front clips and back clips are different.
Add the front assembly to the rest.
You can help yourself with clamps. It should all fit nicely. You can add acetone to glue parts together, but I haven’t done it yet and it holds together since a few weeks of tests.
STEP3:
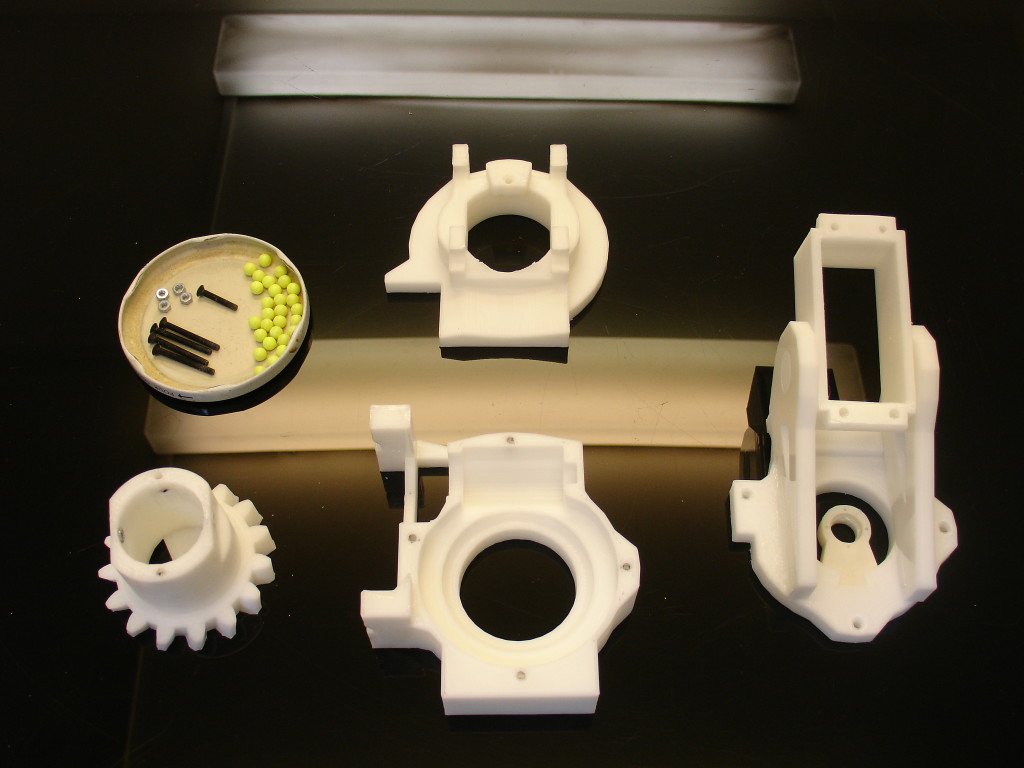
In this part of the tutorial you will see yellow BBgun balls of 6mm.
Carefull with the type of grease you use. Some grease tint the printed parts or even disolve the BBGun balls. The white grease that you see on this picture turned out to be terrible with the plastic BBGun balls, I had to replace all the balls with steel balls.
These of course can be replaced with steel balls instead. Also in this part of tutorial I am using other servo than the HS805bb. These other servo seem to be very good and the price is reasonable. (Ref PDI-HV2060MG)
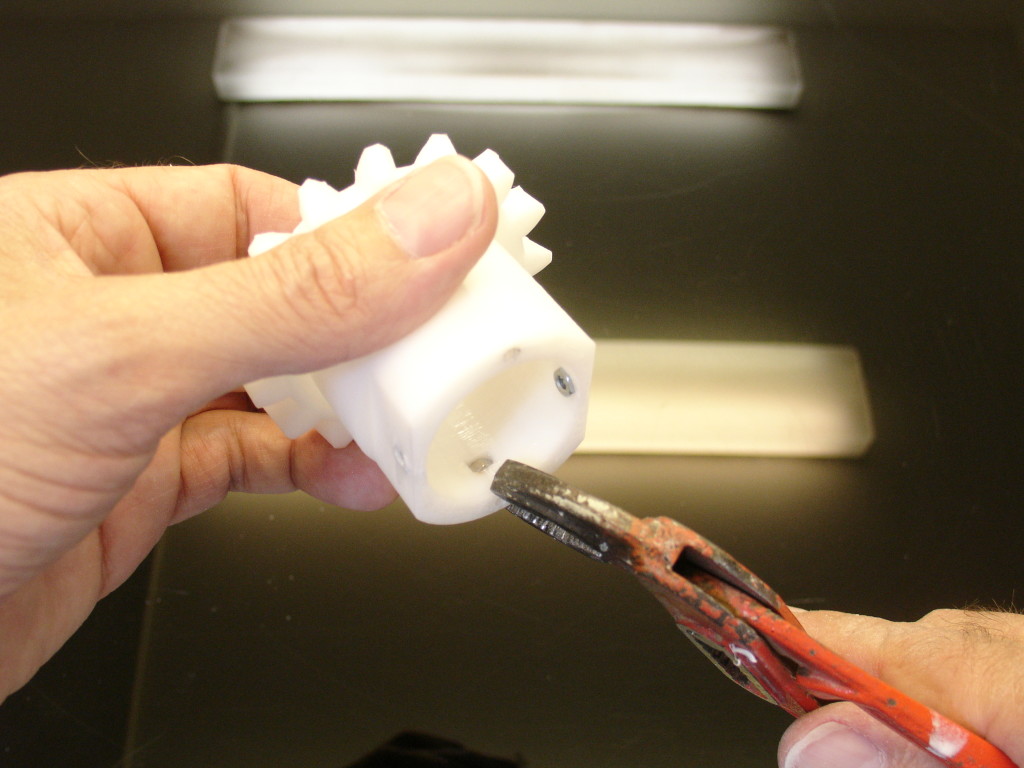
Insert 3mm nuts into each nut shell, these can pushed in with a pair of pliers.
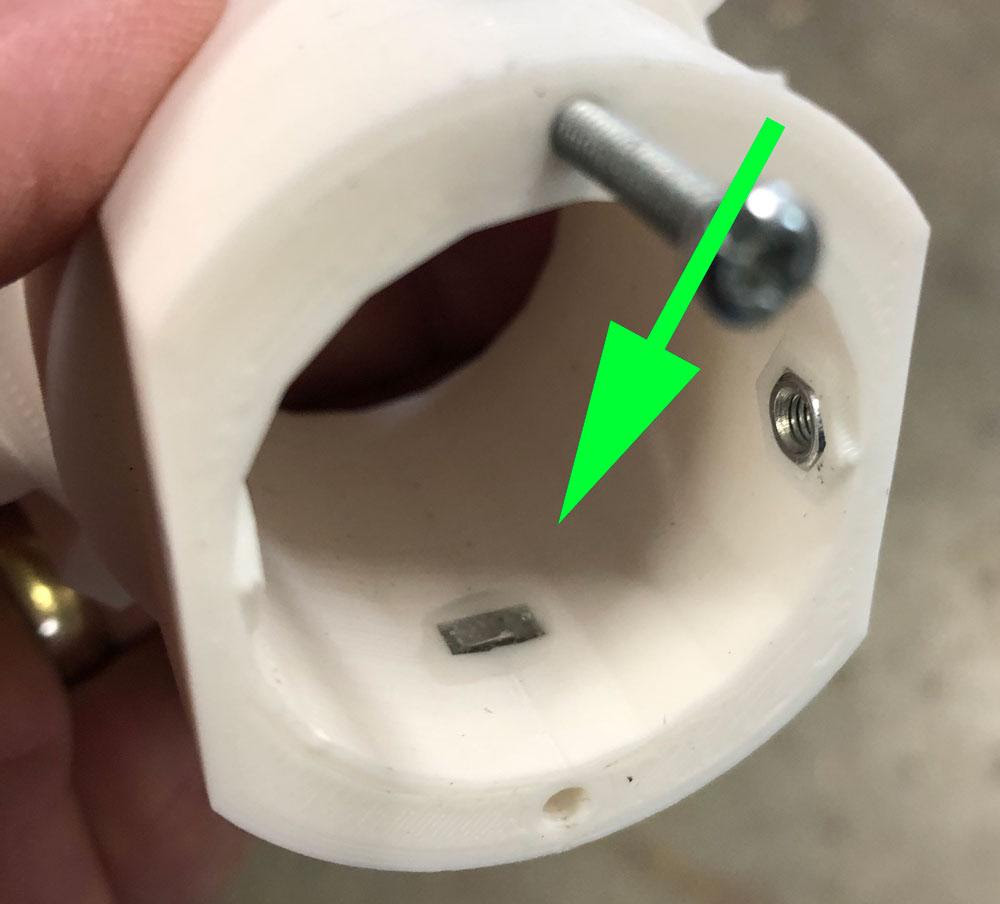
Secure the nut with melted ABS or epoxy glue.
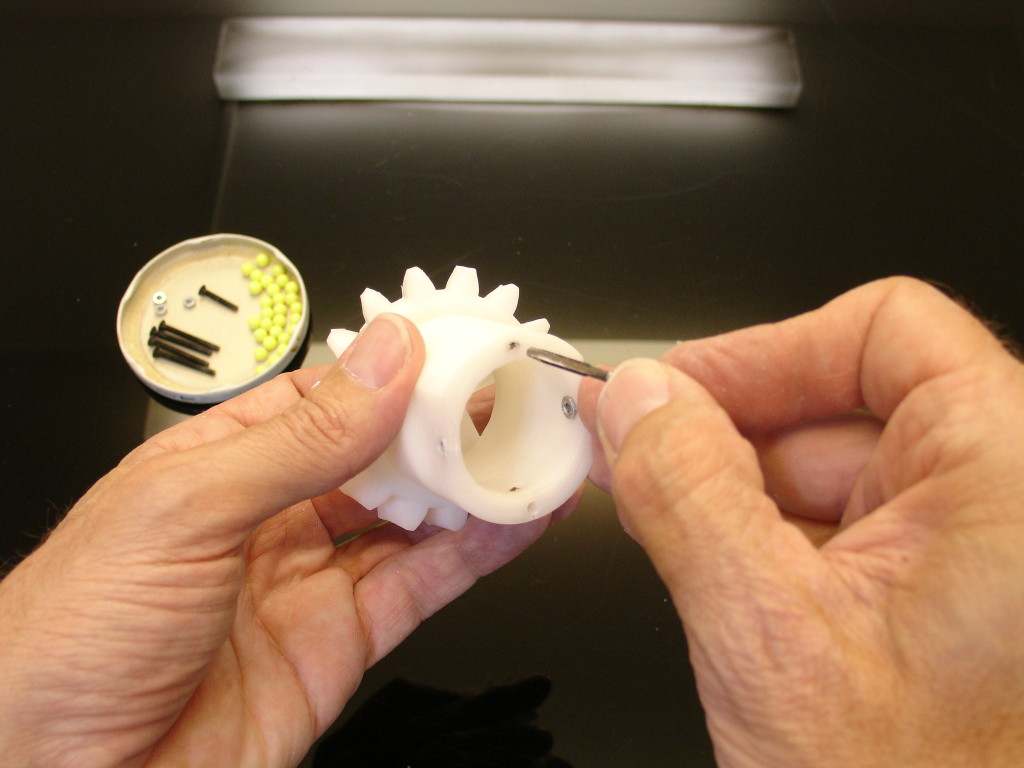
Redrill the holes and make sure your 3mm screw engages correctly into the nut.
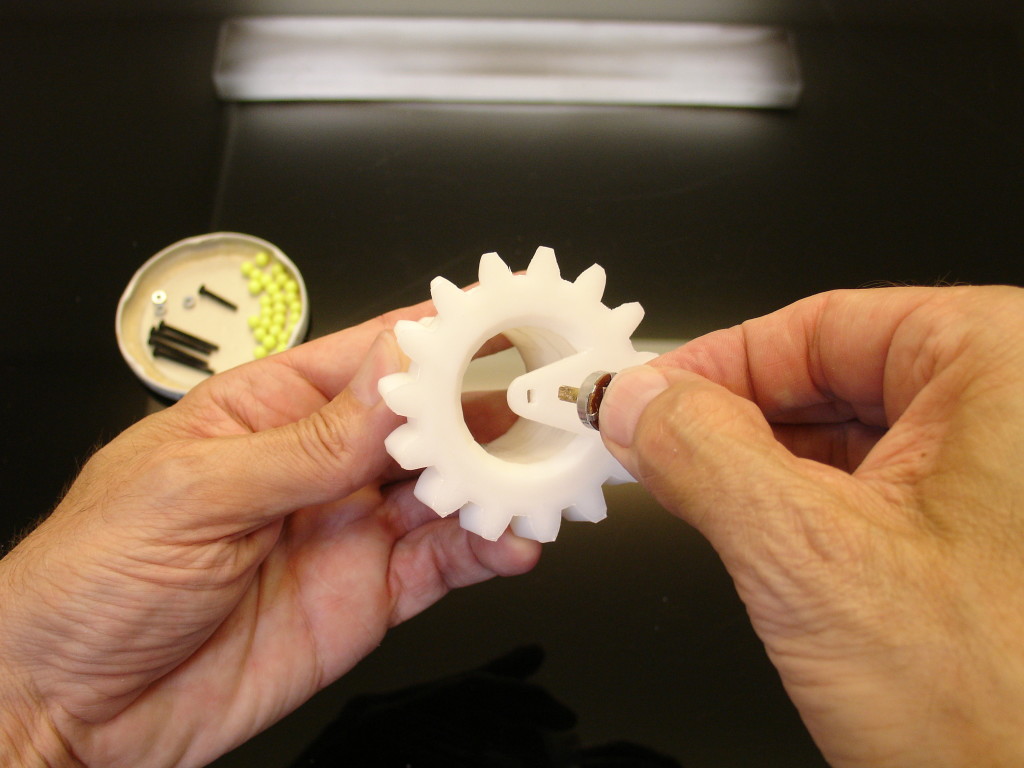
Make sure that the potentiometer shaft fits perfectly into the hole. If necessary use a small file.
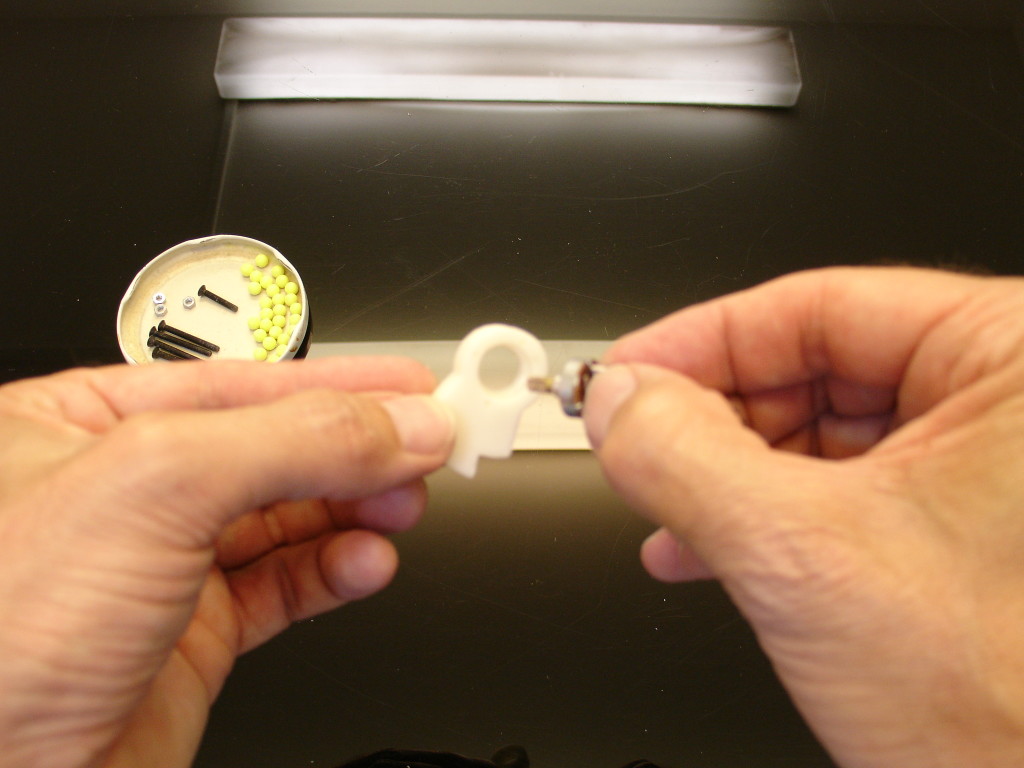
Also make sure the body of the potentiometer fits well into the PivPotentioRound (you might need to use the squary version according to your potentiometer)

Assemble and glue together PivTit, ServoHolder. ServoHolster needs to be inserted but should NOT be glued in order to rotate freely.
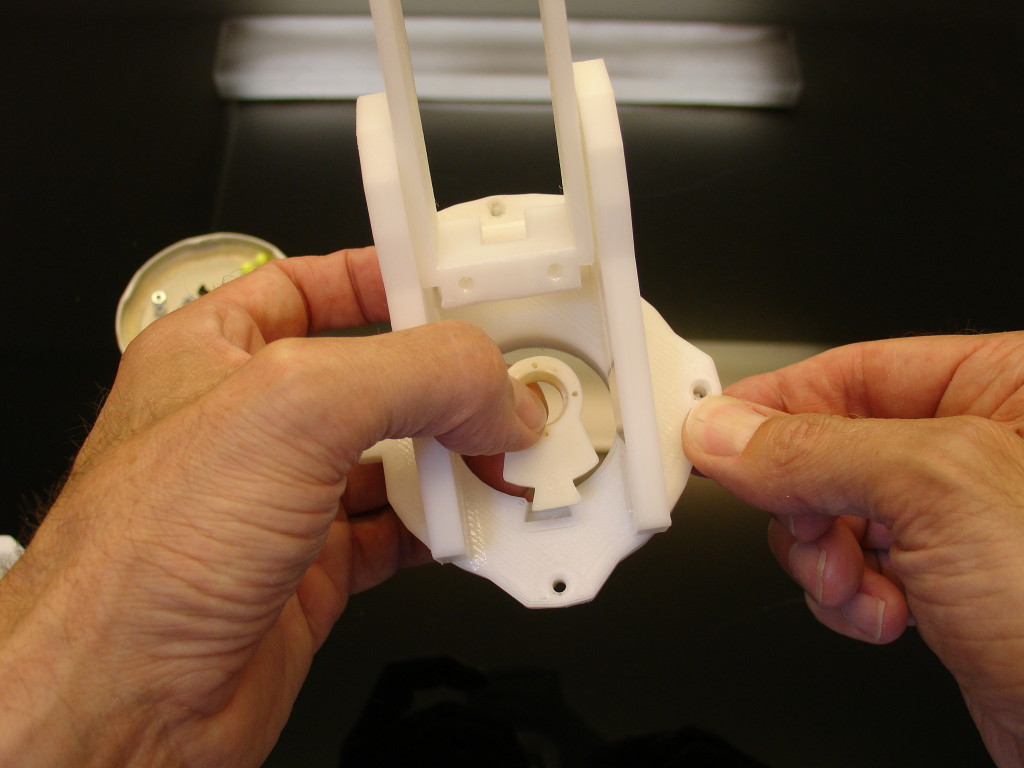
Press fit PivPotentioRound into PivTit. Normally there is no use to glue it.
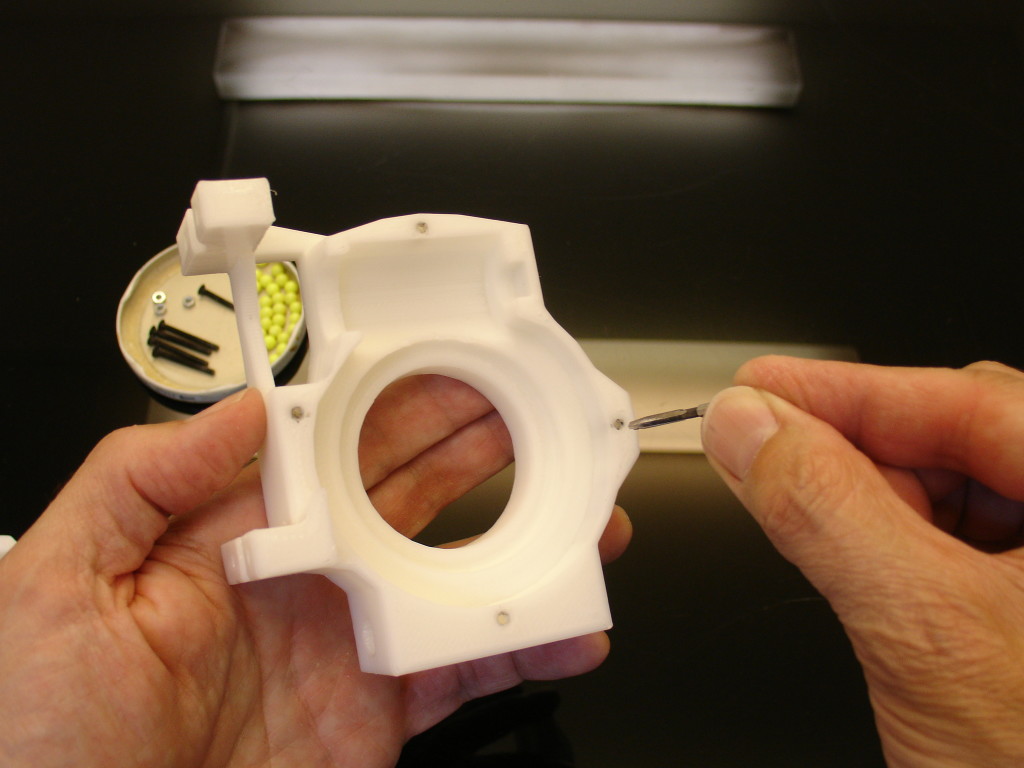
Tab the 4 holes or insert 4 nut of 3 mm on the back of PivCenter.
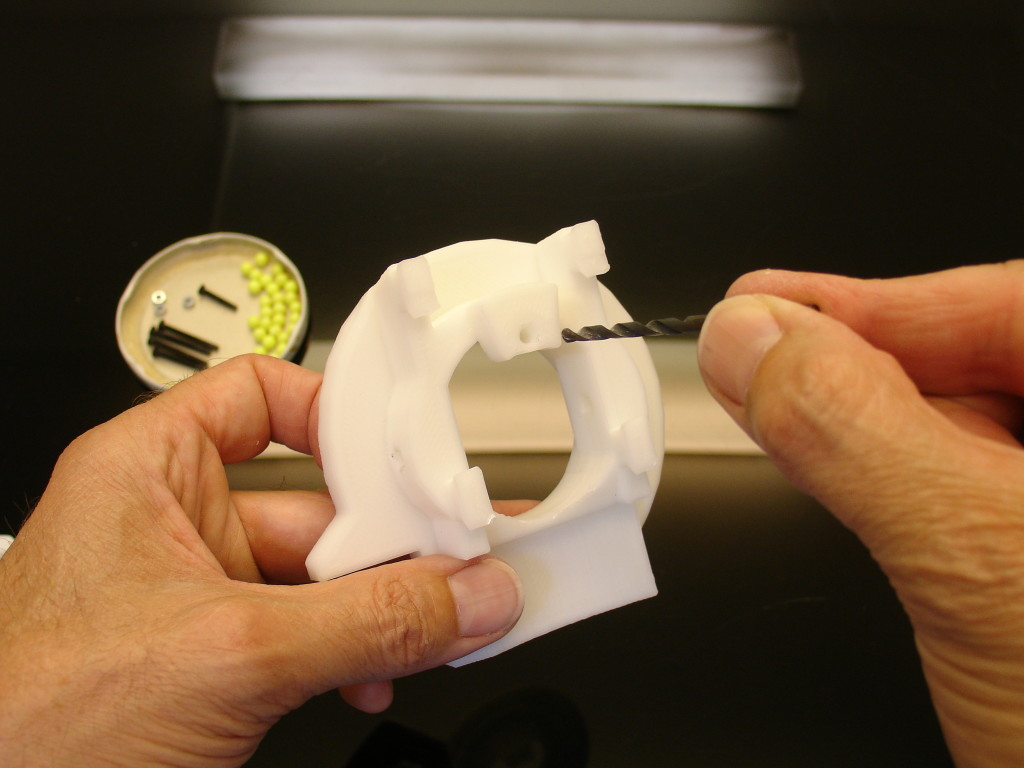
Redrill the holes with a 3.5 mm bore on PivMit.
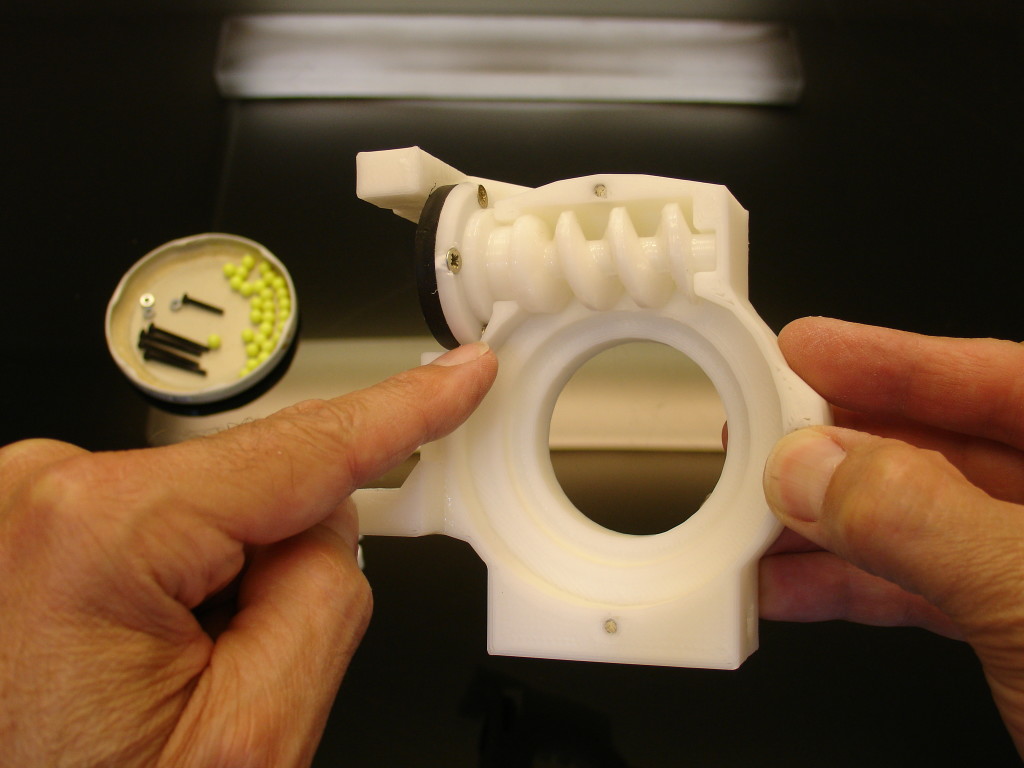
Screw PivWorm to the servo horn wheel(part that comes with your servo). Make sure that PivWorm is well seated in PivCenter and can rotate manually. Also the screws shouldn’t hit the edge that I’m pointing with my left index finger.
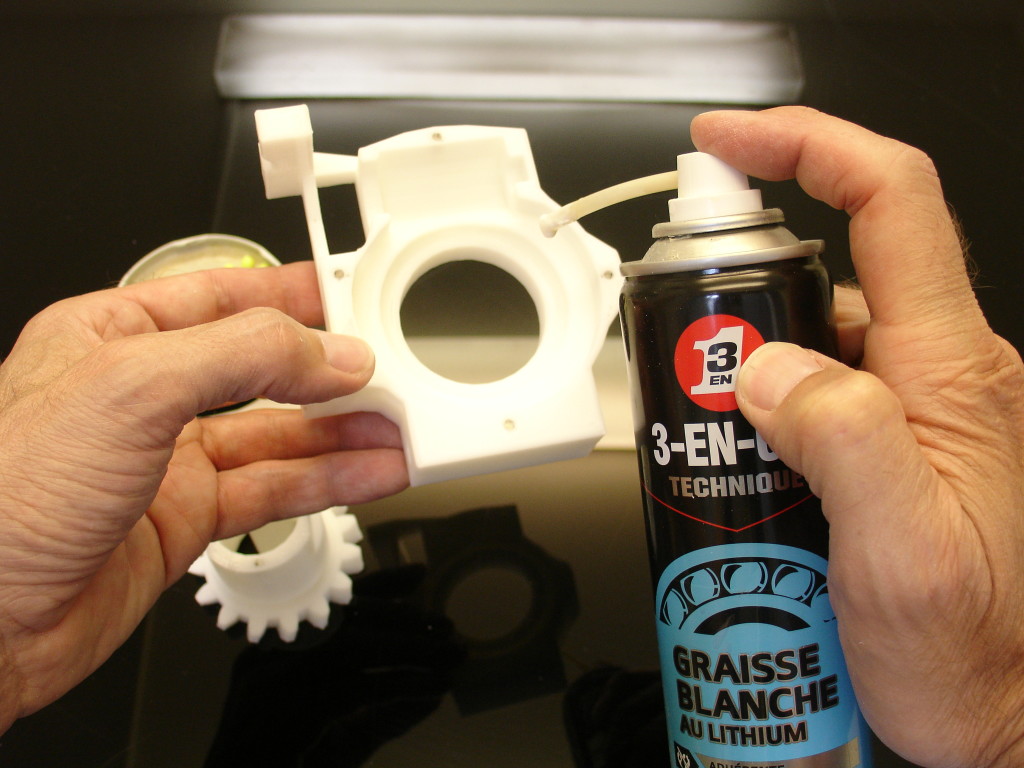
Add grease. Carefull with the type of grease you use. Some grease tint the printed parts or even disolve the BBGun balls. The white grease that you see on this picture turned out to be terrible with the plastic BBGun balls, I had to replace all the balls with steel balls.
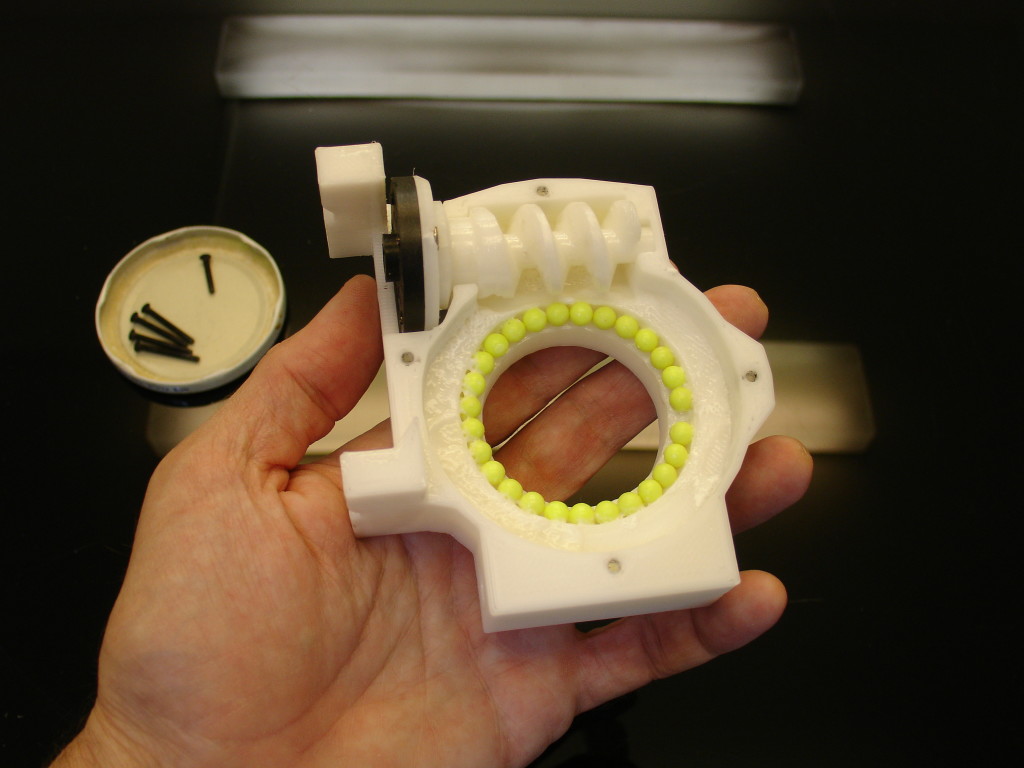
Add the Balls. Here you will need a total of 27 balls.
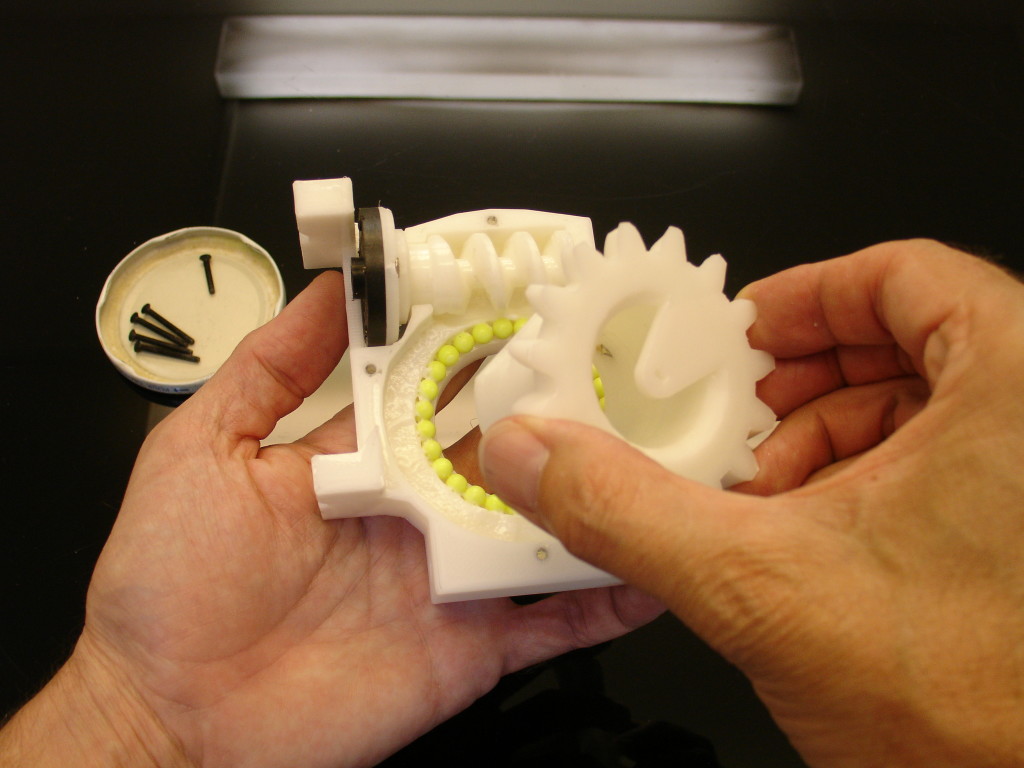
Insert PivGear.
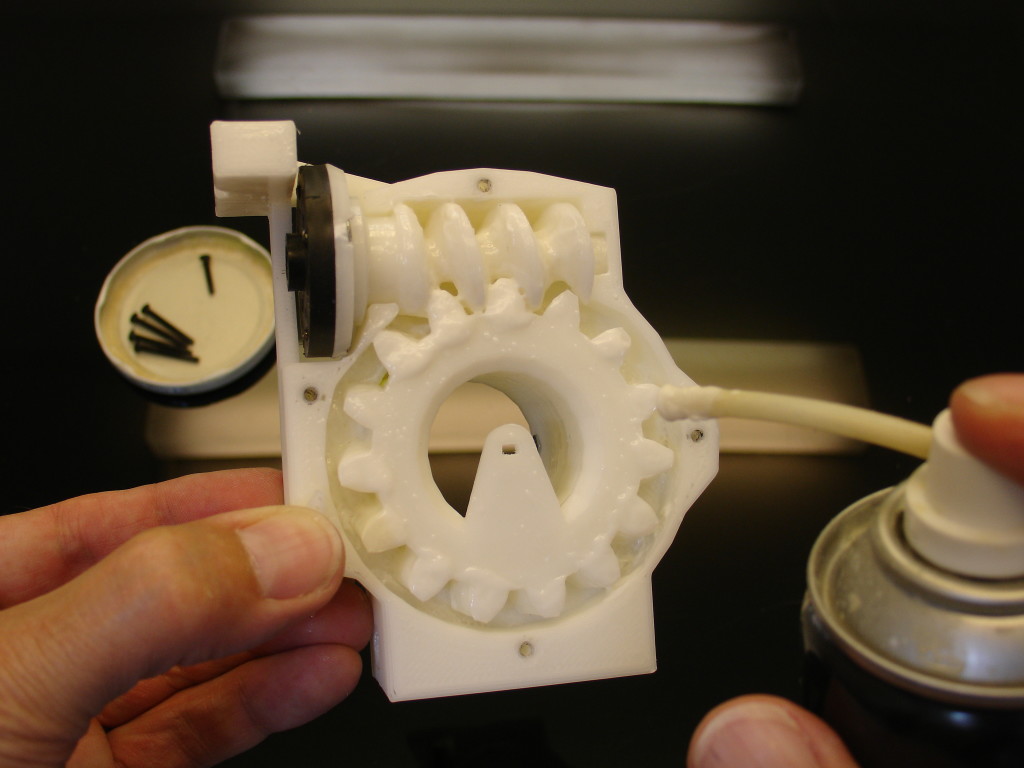
Add more grease everywhere on the teeth. See how PivGear is positionned on my picture, make sure it will be turned this way when we will later add the potentiometer.
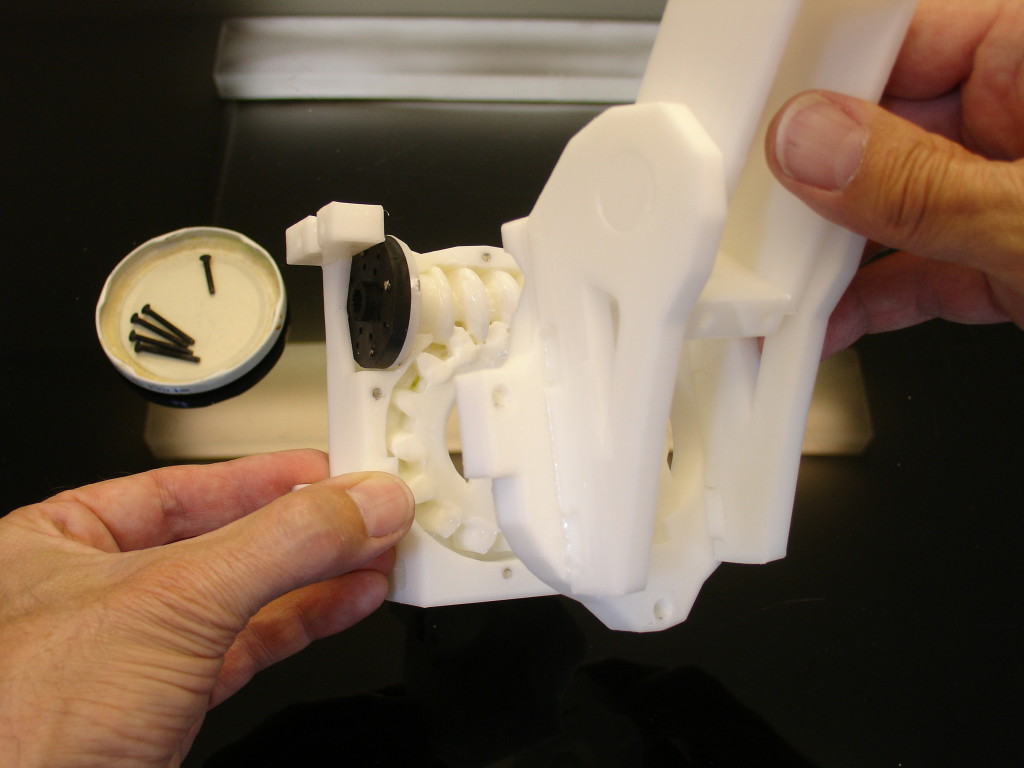
Mount PivTit.
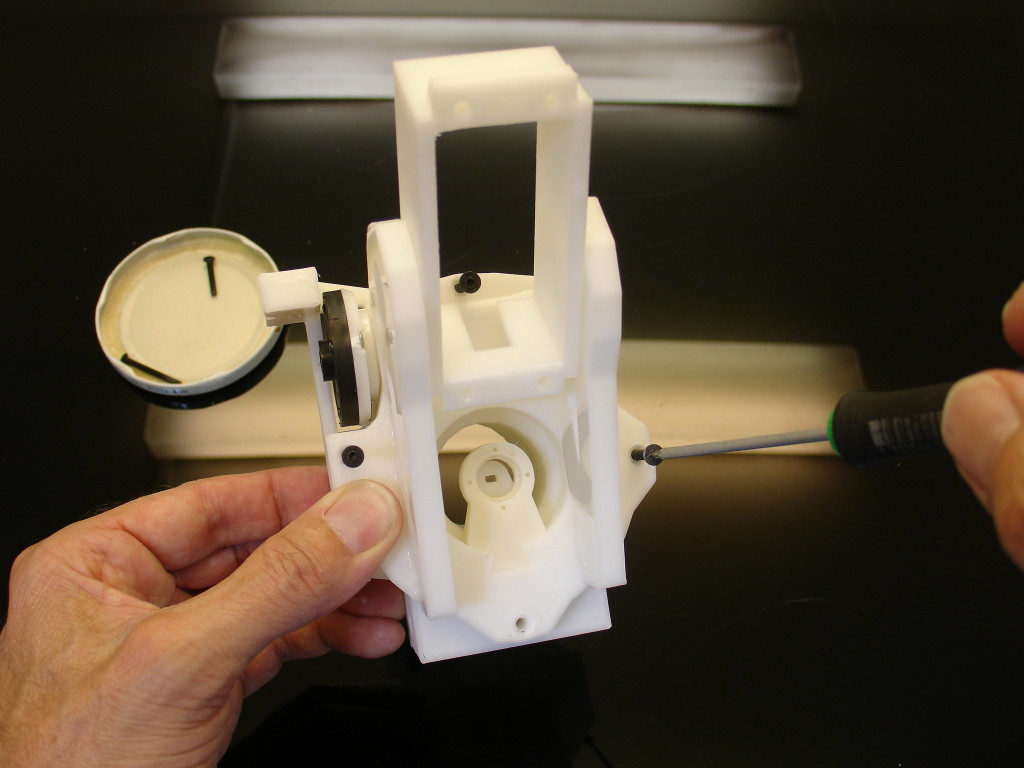
Screw PivTit to PivCenter with 3mm screws. I use hexagonal screws with a length of 35mm to reach the nut on the other side of PivCenter.

This screw needs to be shorter (20mm maximum) in order to let the 8mm shaft rotate freely.(Chrome shaft in this picture)
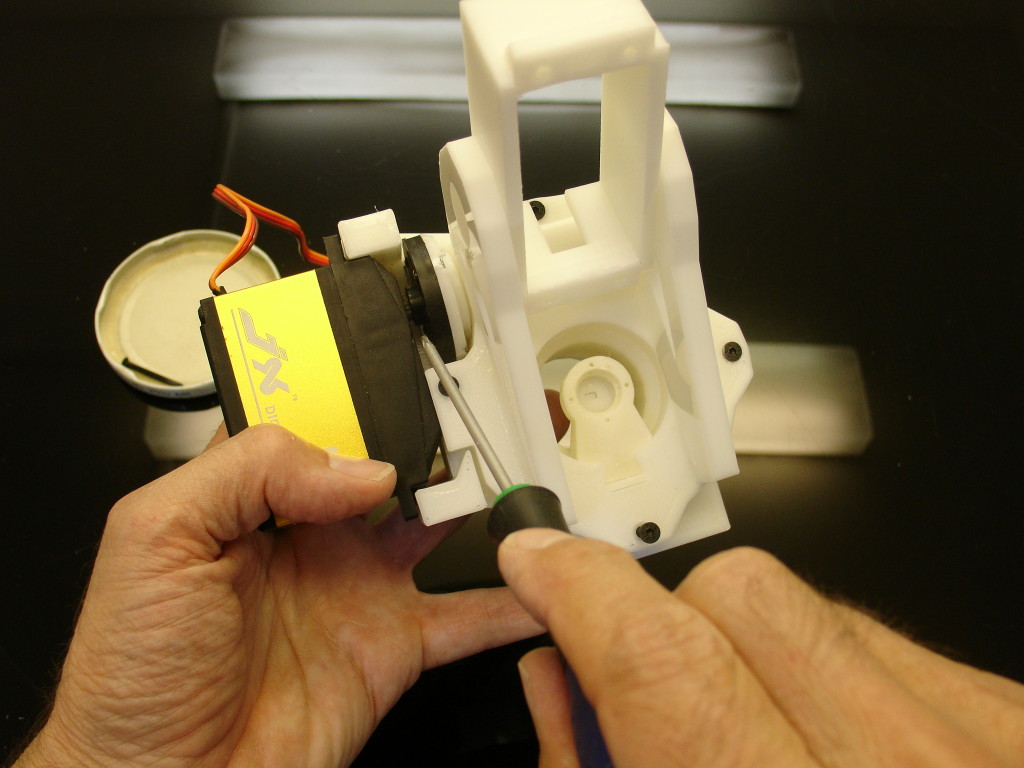
Engage the servo on the servo horn wheel. Make sure it is fully engaged, some horns are a bit nasty and hard to manually press fit. So don’t break something. As you see in this tutorial, I am using another model of servo than the HS805BB and it was really hard to press fit.
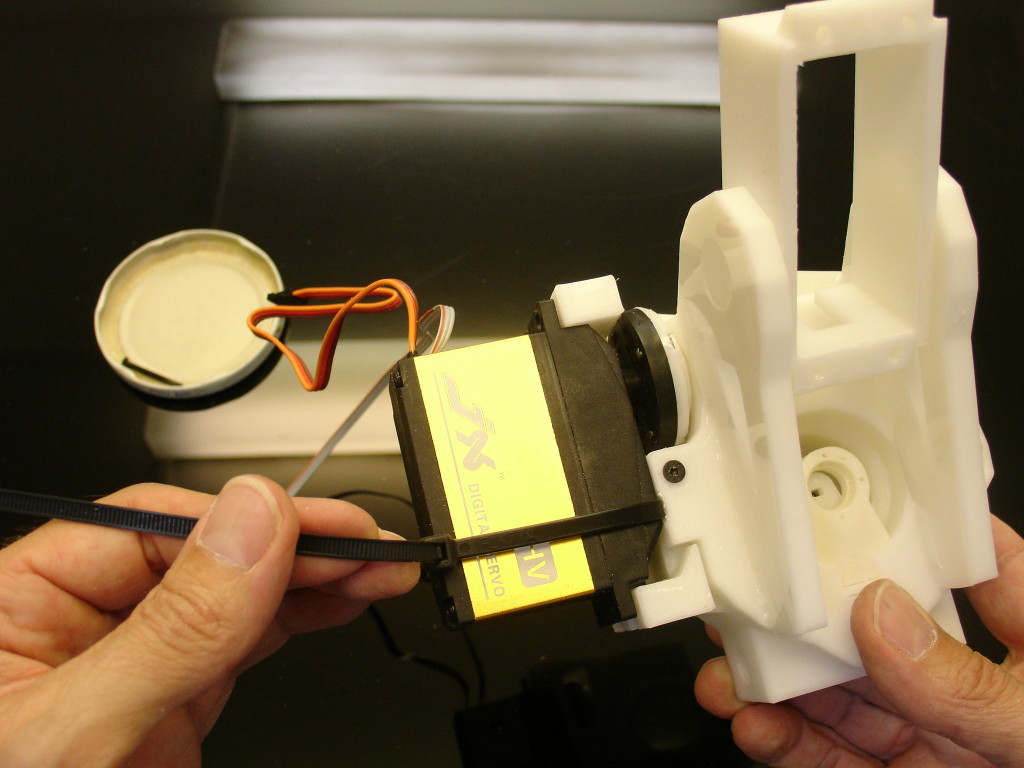
Prepare and add a plastic zip around the servo, see how and where the zip connector is placed, it is important to do the same for futher assembly. Don’t tight completely the zip yet, we will pass through the ribon and cables later.
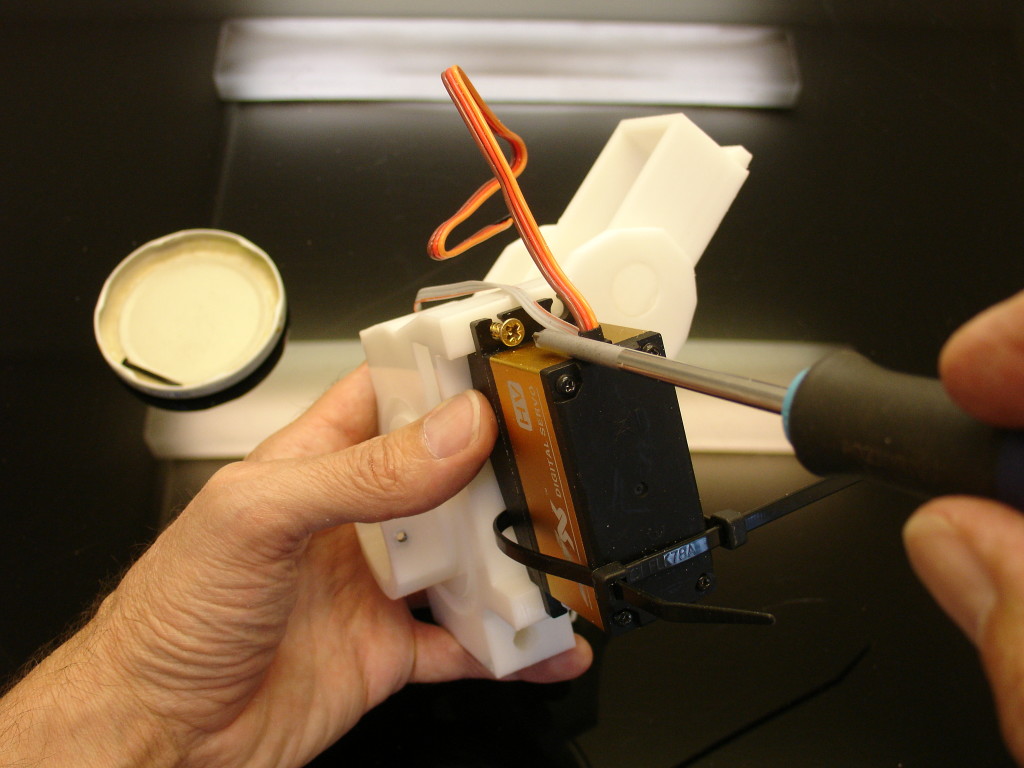
Now you can add the 4 screws to fix the servo. I use standard Philips wood screws of 3,5 x 16 mm but you can fit other sizes as well.
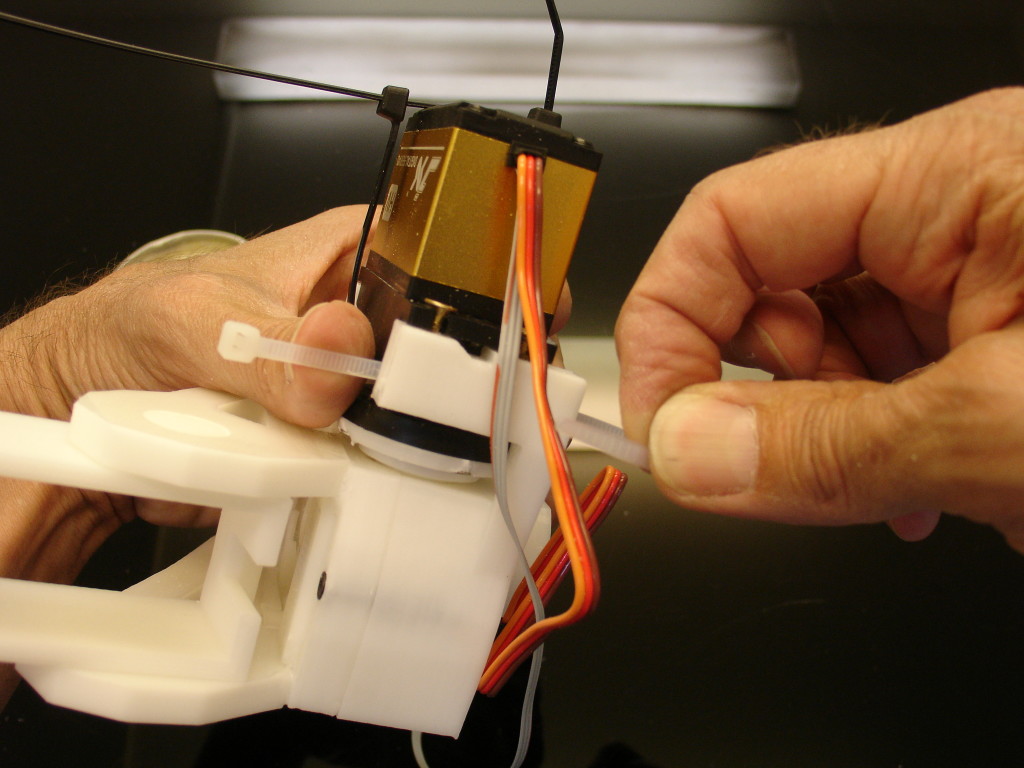
Insert another plastic zip as show.
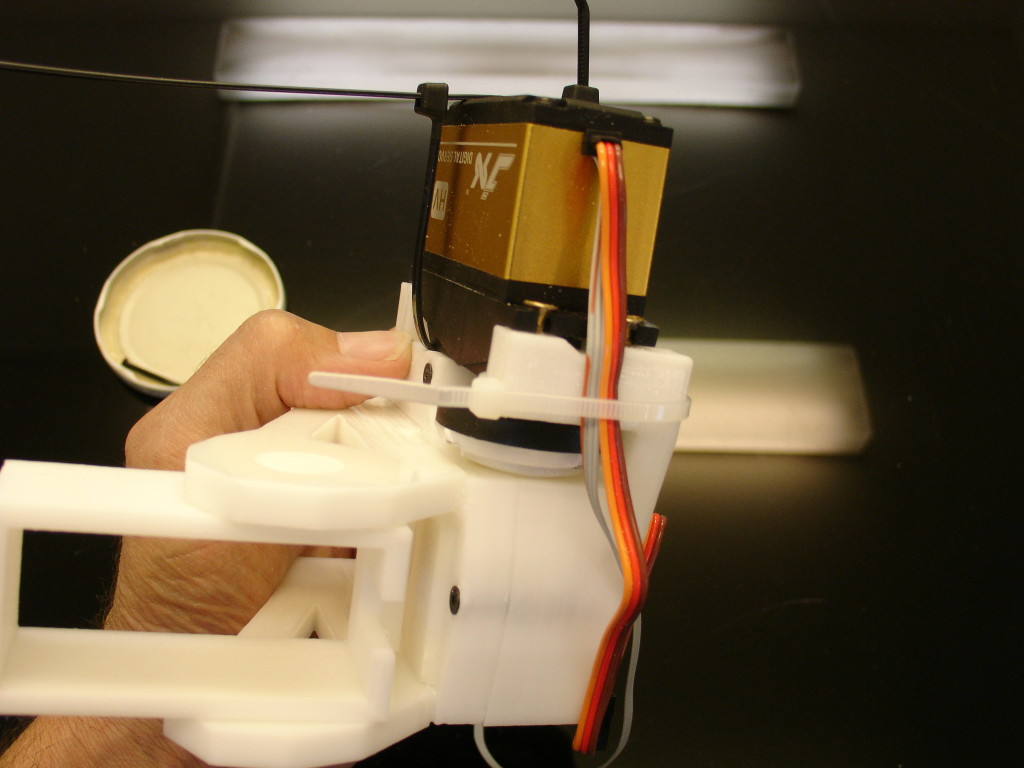
Pass through both cables coming out of your potentiometer. (servo and potentiometer extension)
You can tight the plastic zip, respect its position as show on the picture. Cut the extra zip length.
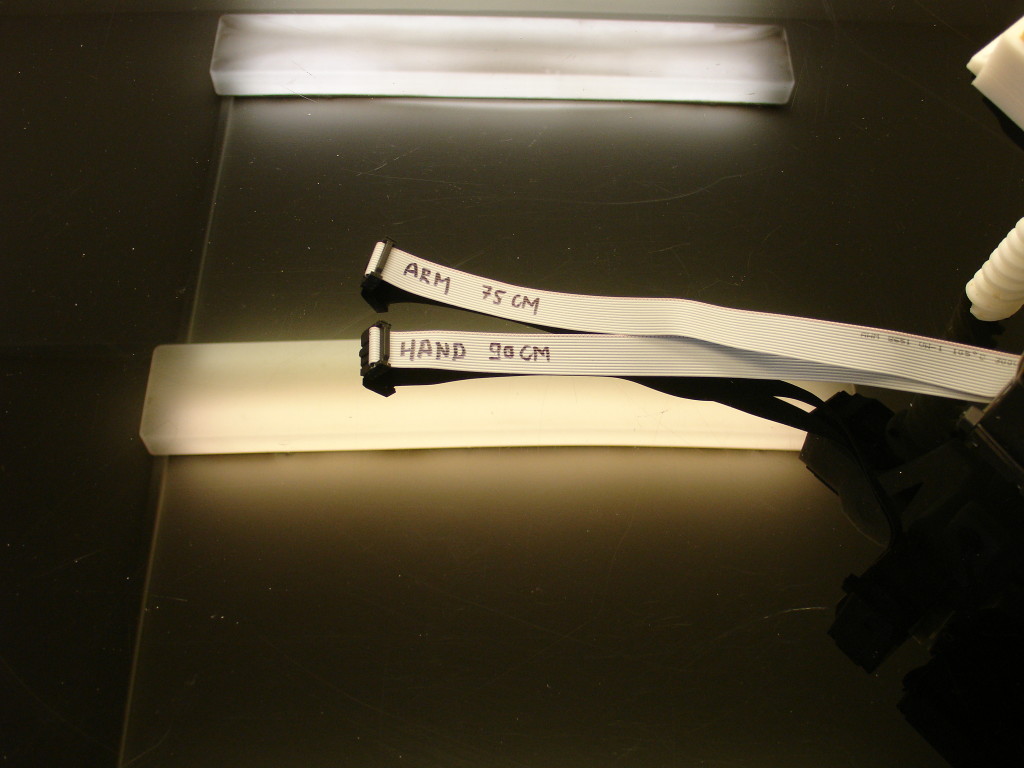
Now lets prepare and cut the ribon cables for the arm and hand. You can see the necessary length noted on the ribons. Do not fix the headers yet!
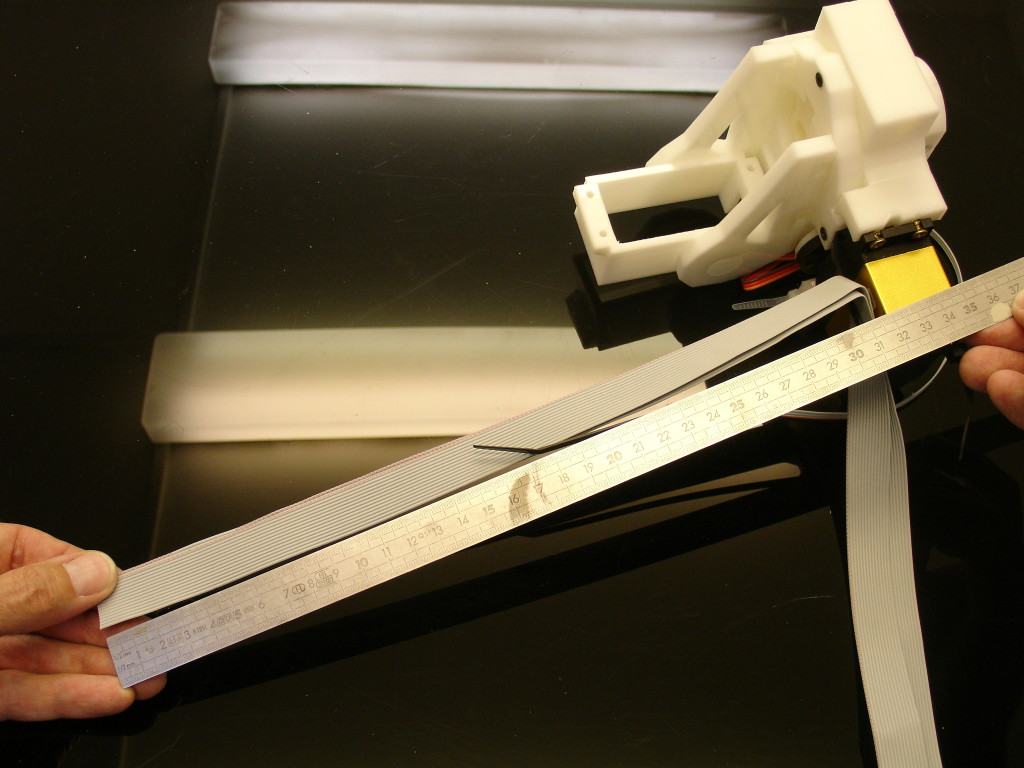
Fold both ribbons at approximatively 30cm, and pass them through the black plastic zip. Note on my picture how the red lining(Vcc+) of the ribbon is set.

Fold again the ribbons and pass them through the second white zip. Fold once more the ribbons and run them down as shown on the picture.
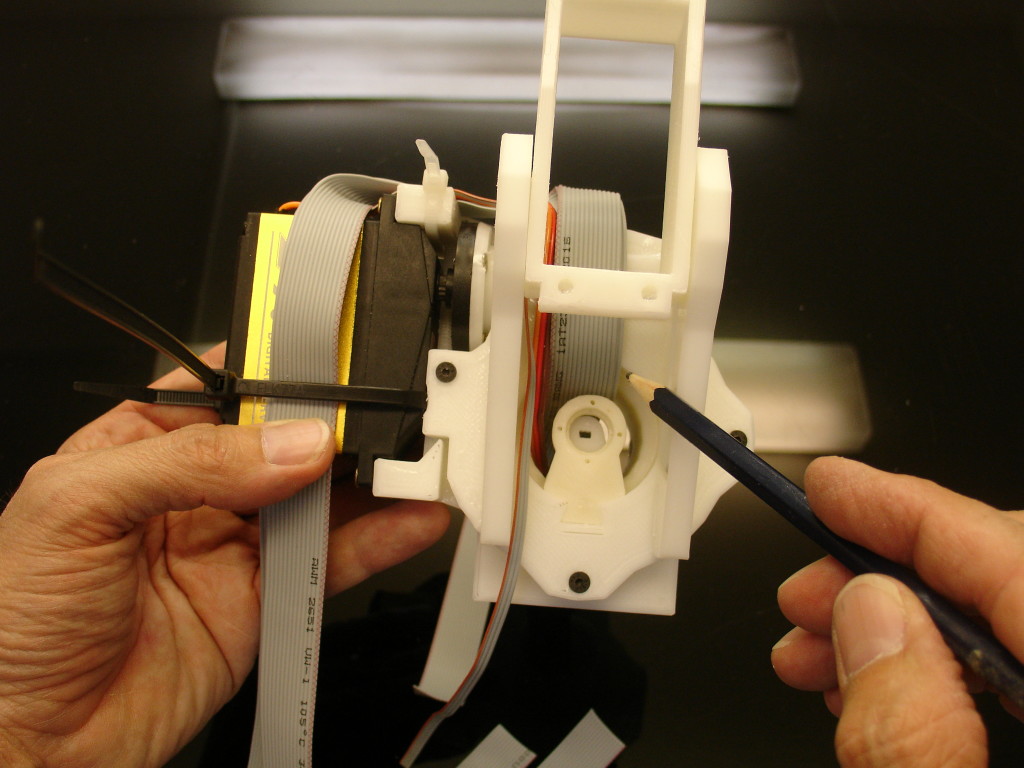
Now pass both ribbons and the servo cable through PivGear as shown.

You can see here I am holding the cable for the potentiometer which doesn’t need to run through PivGear. (As info: when I prepare the extracted potentiometer, I add a 35 cm extention of cable which is largely enough as you can see.)
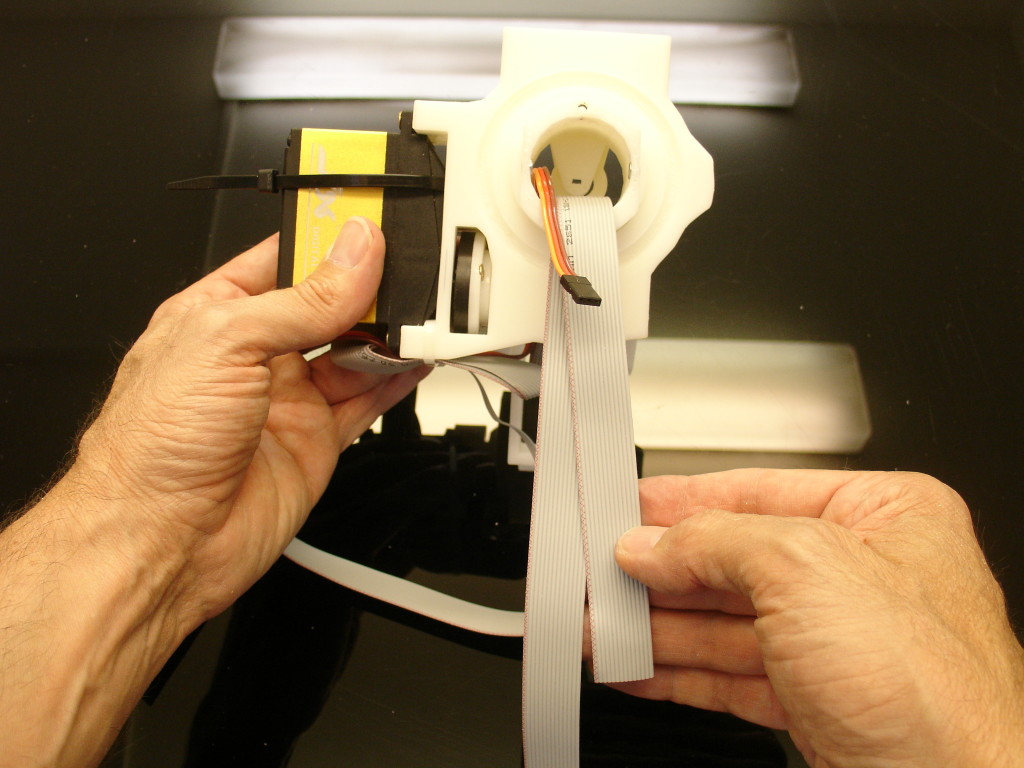
From the other side it should look like this.
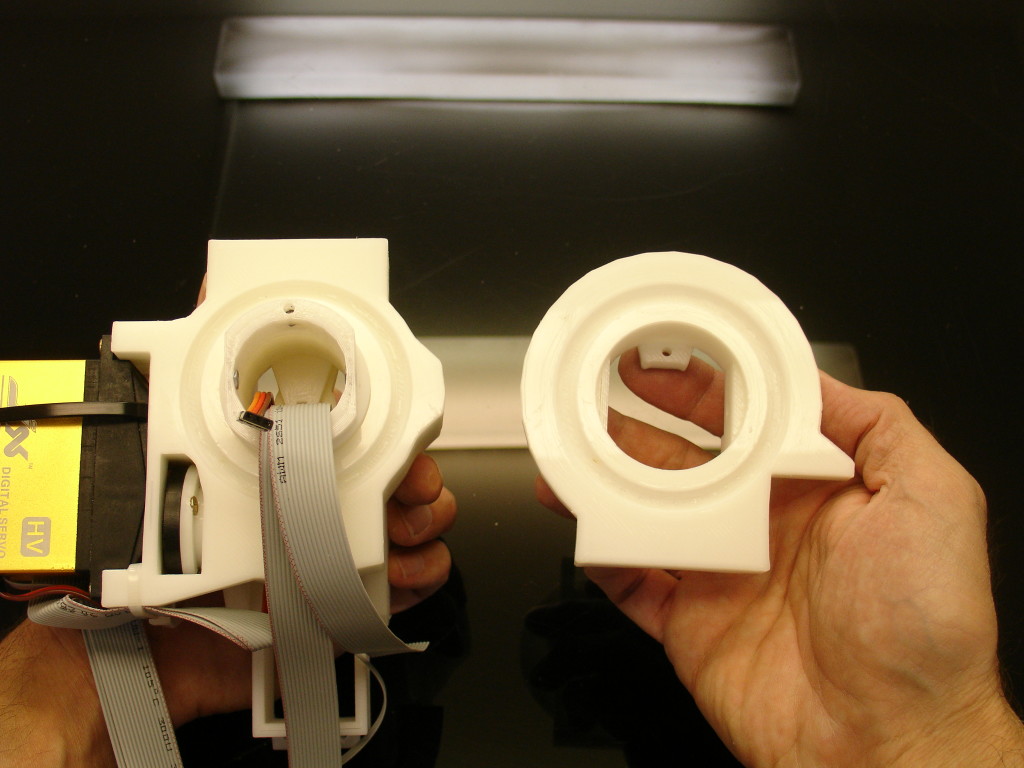
Get PivMit part.
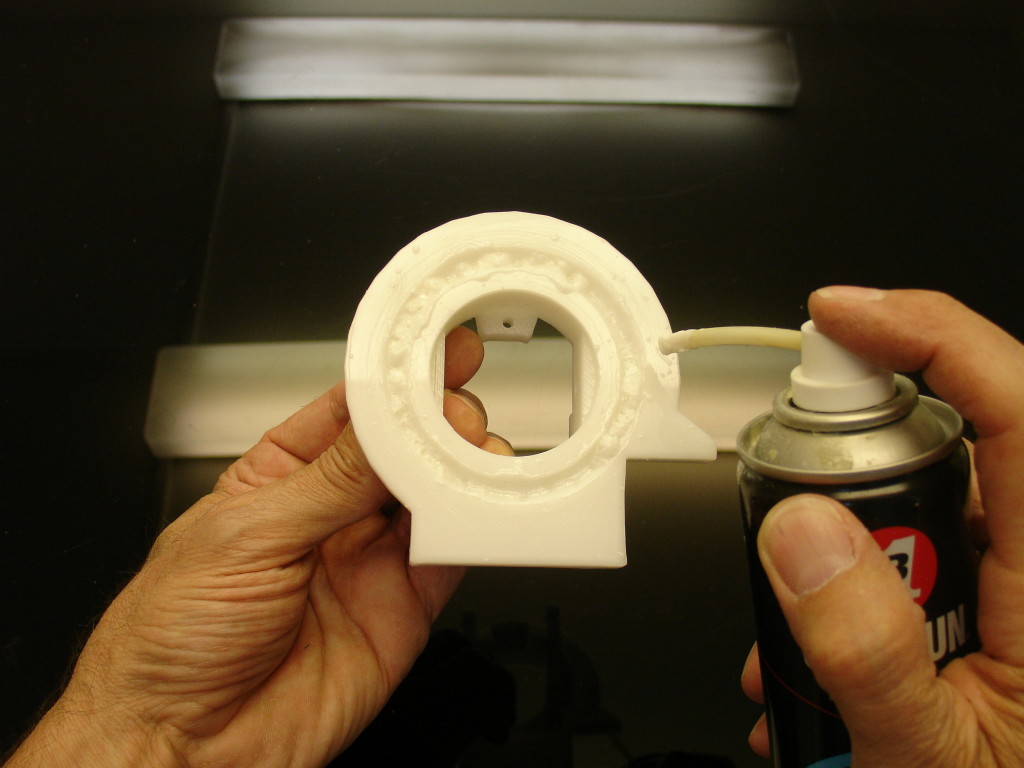
Add grease on PivMit in the ball joint.

Add 31 balls.
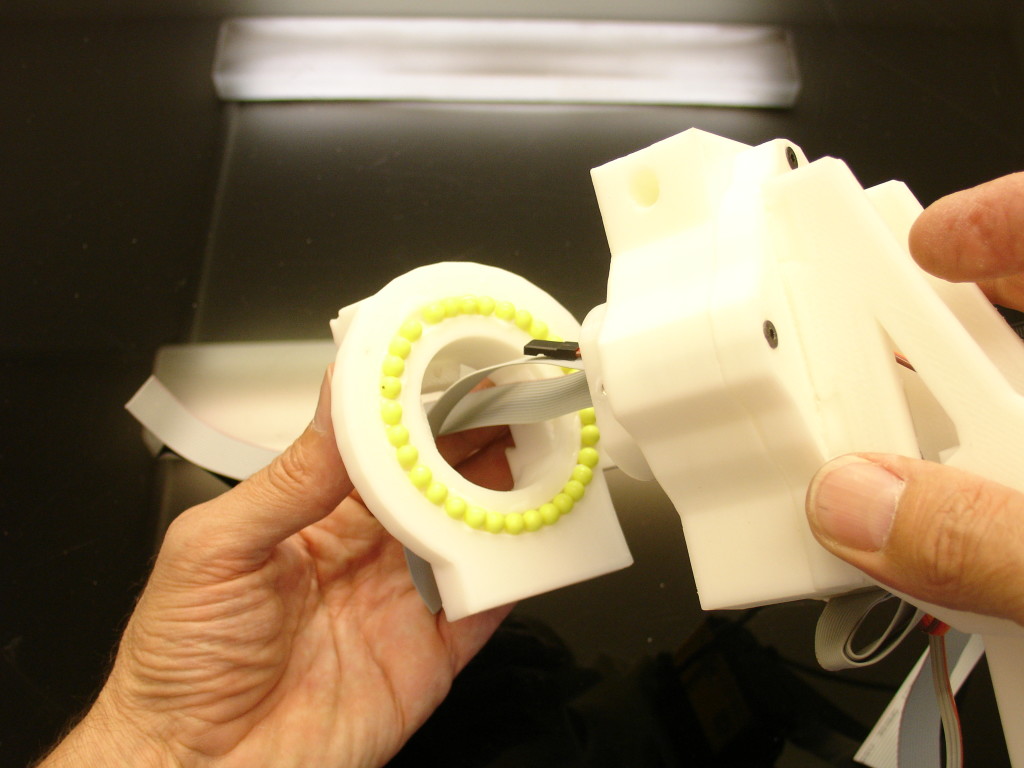
Insert PivGear into PivMit as shown on the picture. Be carefull not to put it upside down.

Add WITHOUT tightening a 3mm screw of 30mm length to reach the nut. This screw is to adjust the pressure on the ball bearing.
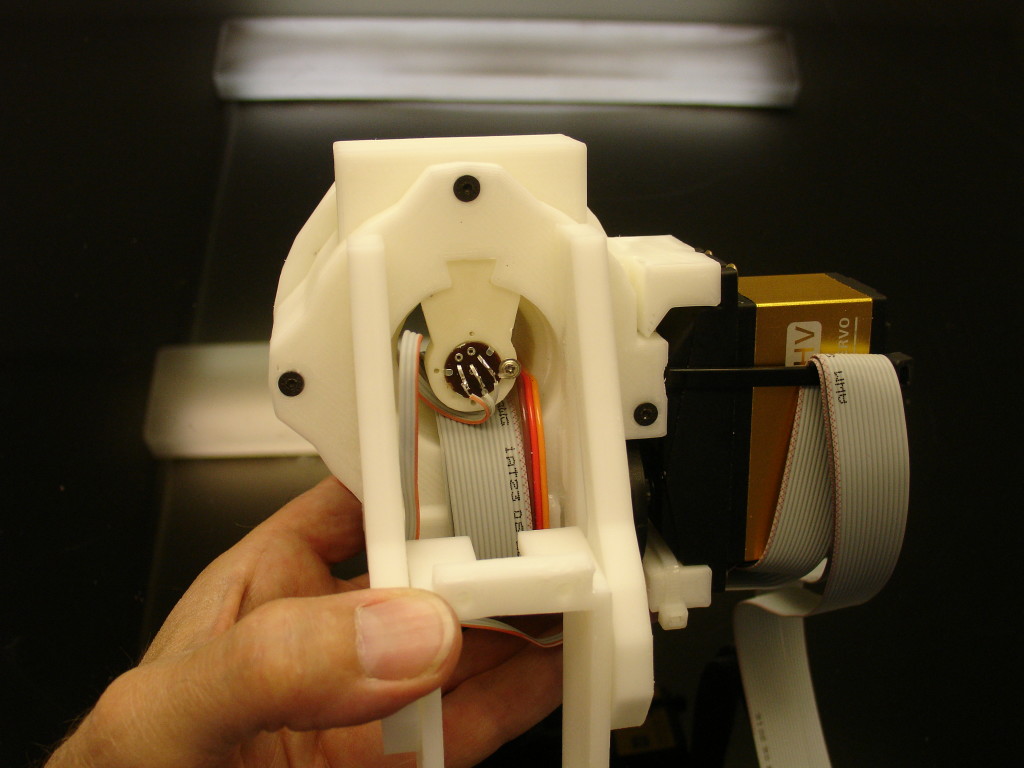
Now we can mount and solder the cable to the potentiometer. Note the slight rotated position of my potentiometer, your should be approximatively the same. Later you might need to re-adjust its position.
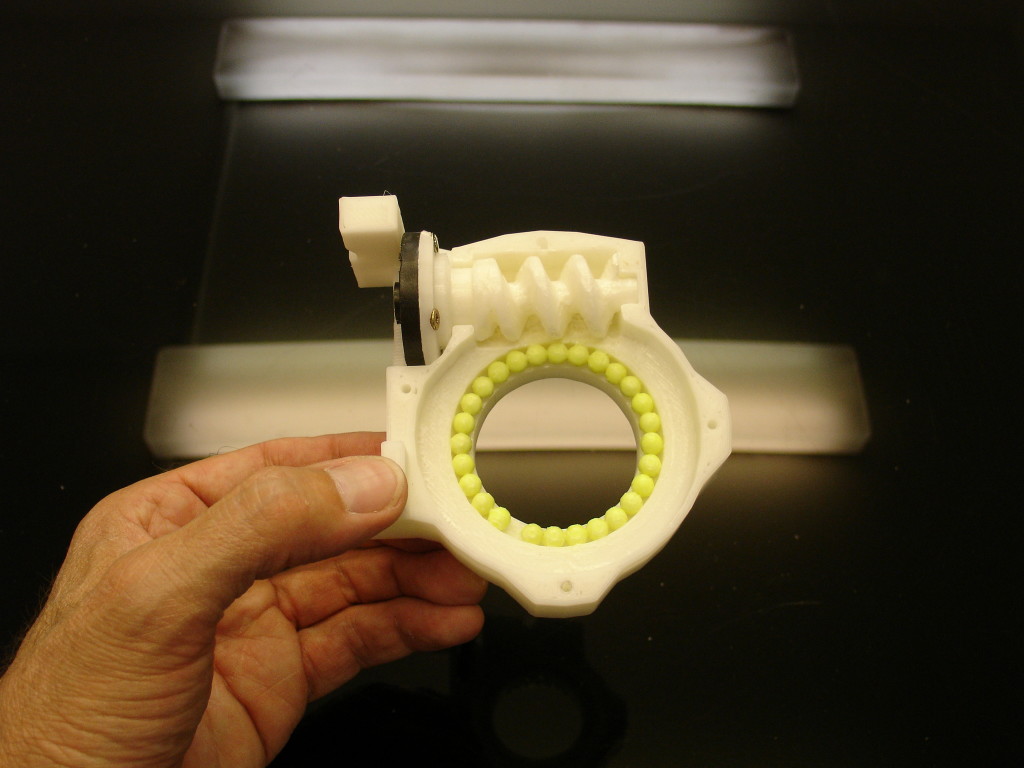
Lets prepare RotCenter with grease and 27 balls. Lets also prepare RotWorm screwed on the servo horn wheel.
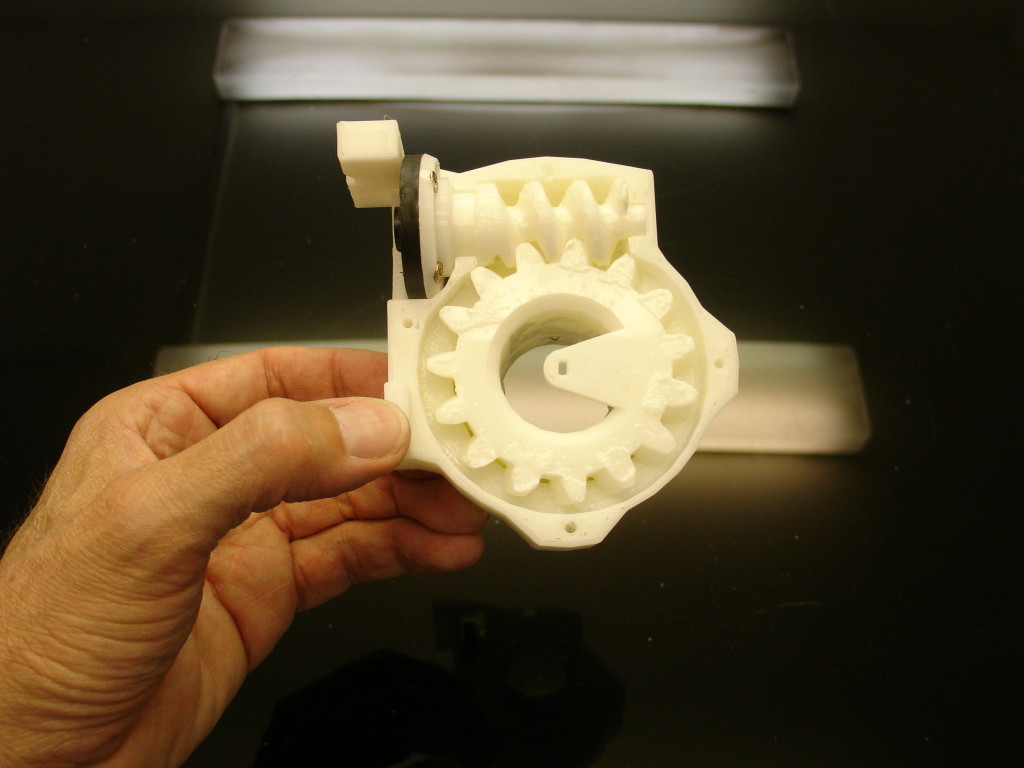
Lets add RotGear and grease. Note the position of RotGear on my picture.
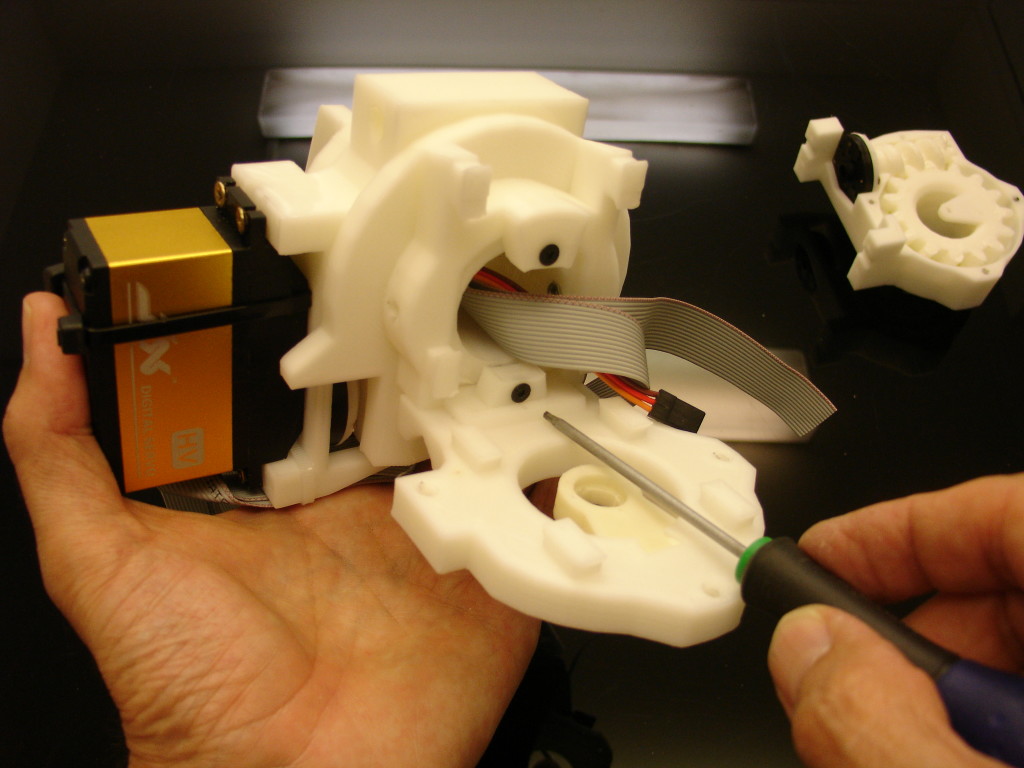
Mount RotTit as shown to PivMit. Do not over tight the adjusting screw, it is only meant to adjust the pressure on the ball bearing. Press fit PivPotentioRound into RotTit.

Mount PivConnector, use pliers to press fit them. In case it is very hard to fit them, you can use a heat gun to gently soften up the parts. (With a well calibrated printer, the parts just fit perfectly)
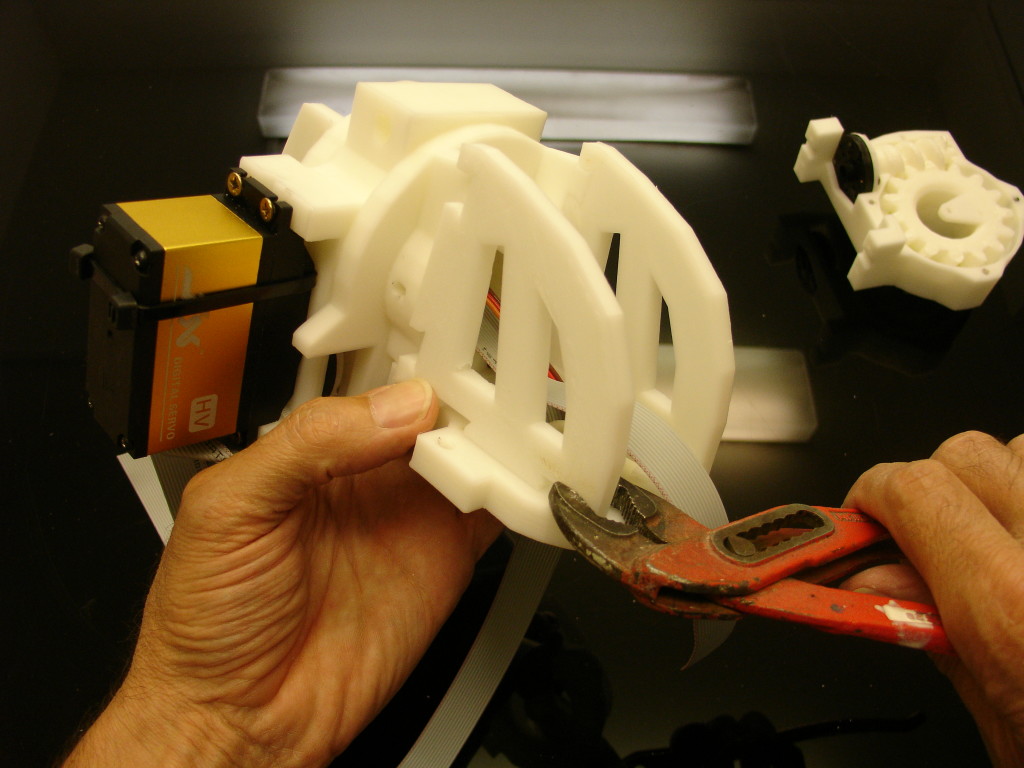
Mount the second PivConnector. Glue with acetone all four parts together, and do it well, this is going to take a lot of pressure.
Mount RotCenter to the whole assembly as shown. Make sure that RotGear is still in the correct position as shown.
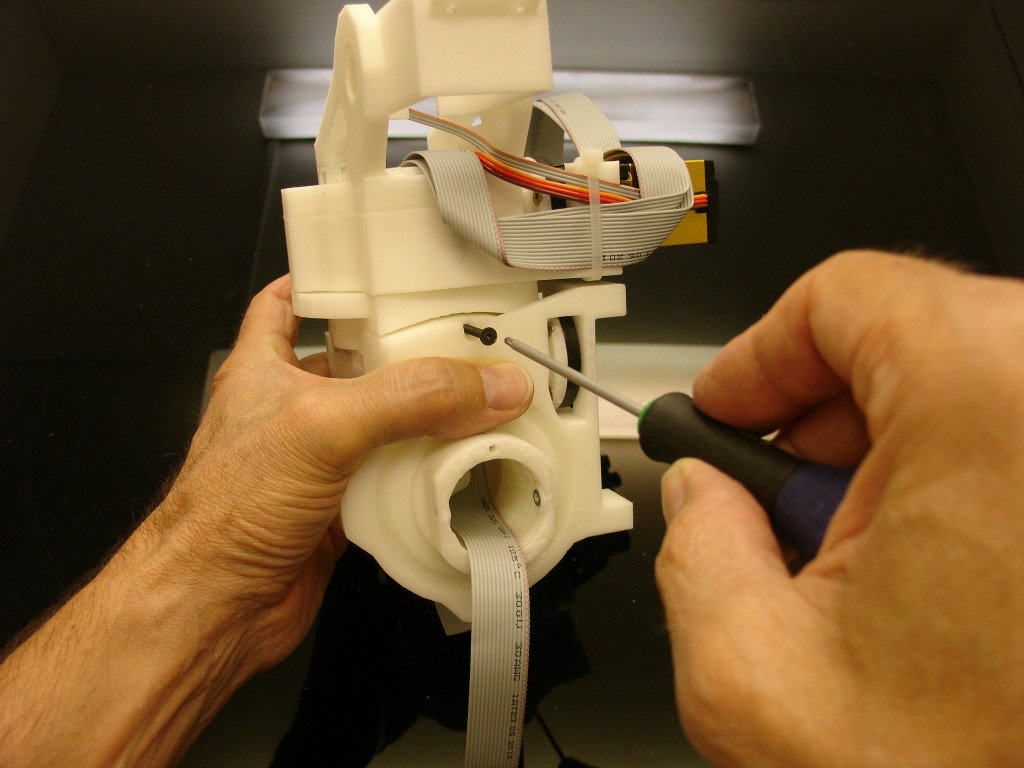
Add a 3mm, length 30mm screw through the bottom of RotCenter to reach the nut on the other side.
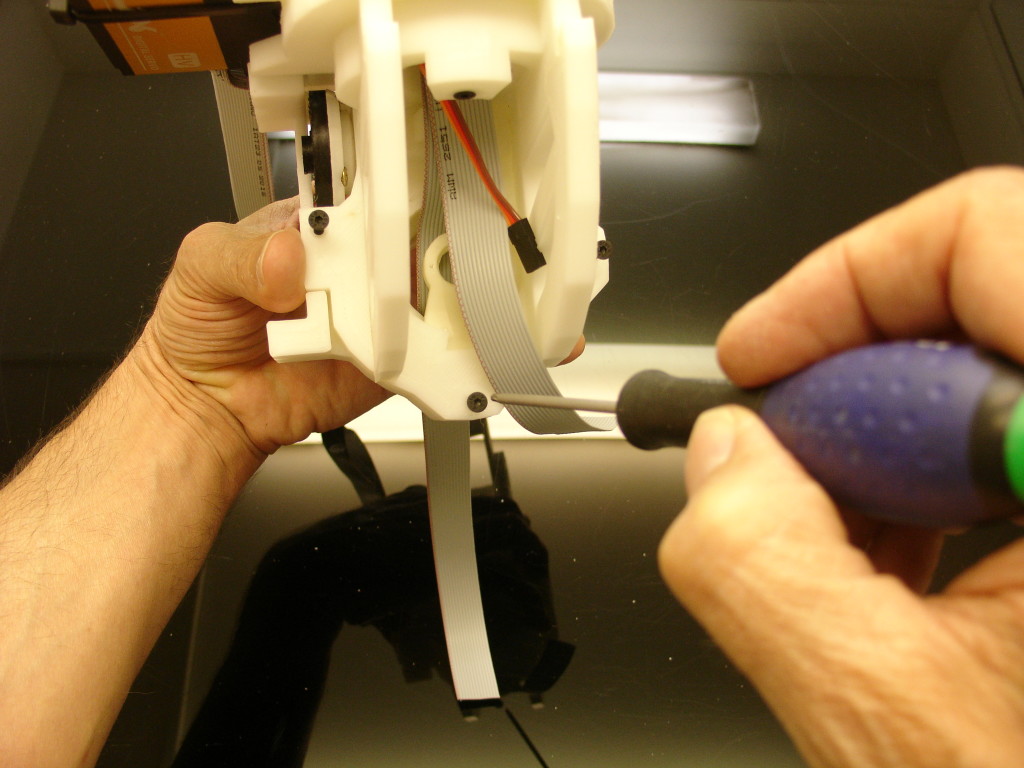
Add the other three screws of 3mm, 30mm length by the top as shown.
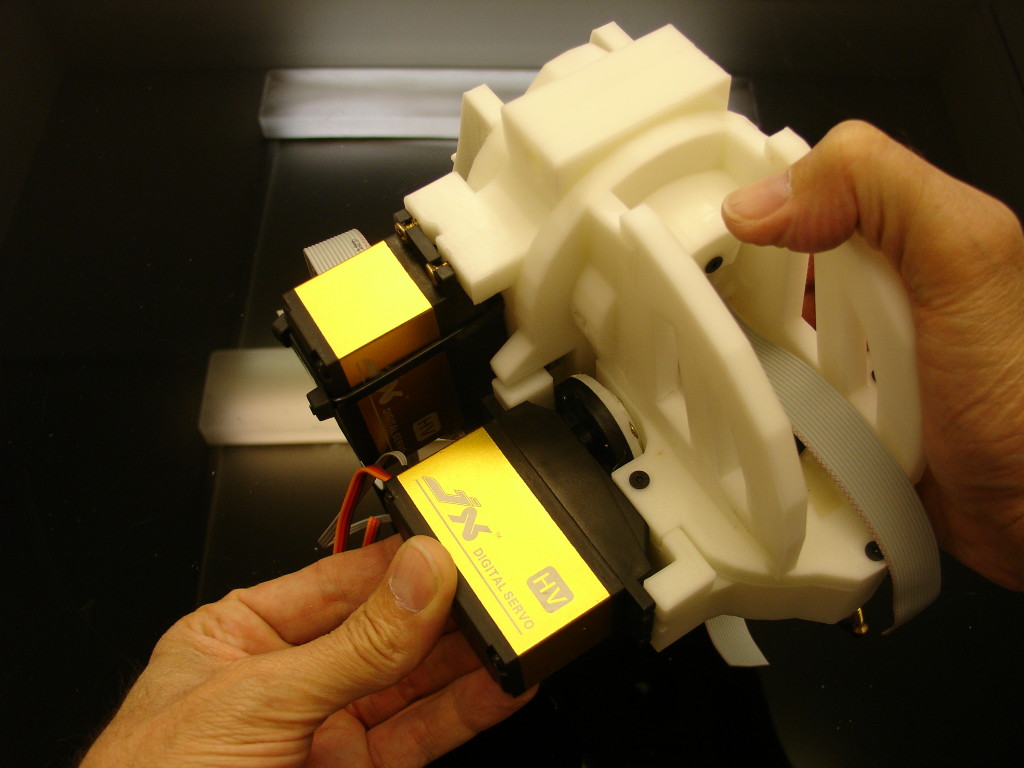
Time to mount the second servomotor.
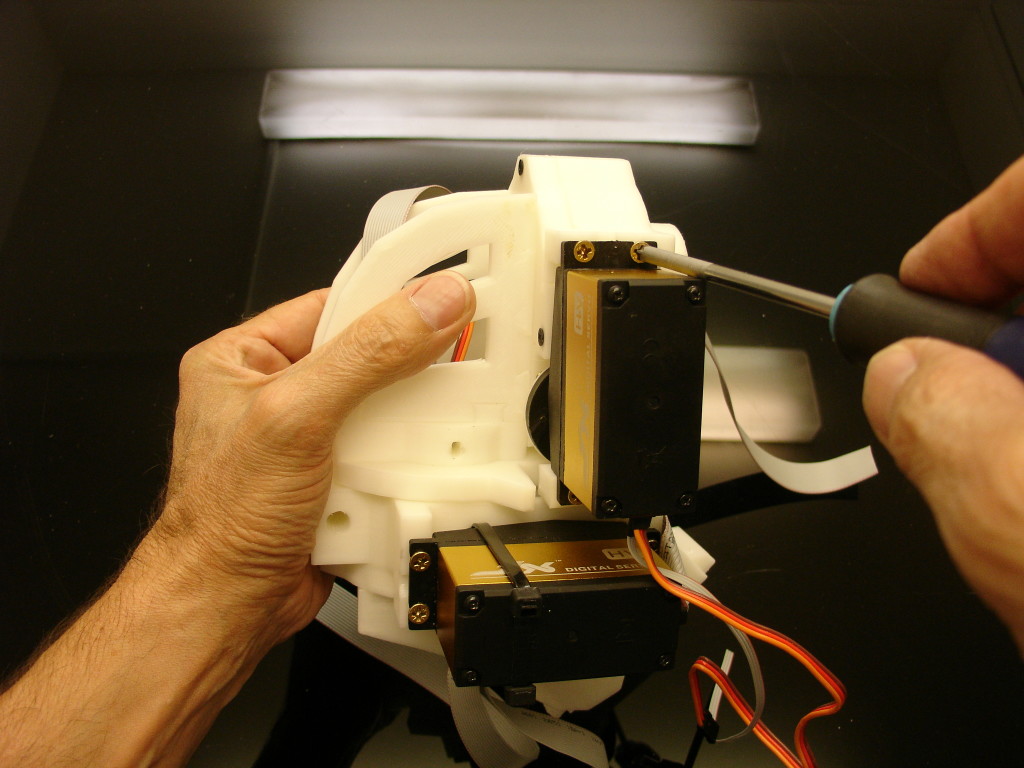
Add and tight the four standard wood screws 3.5mm x 16mm.
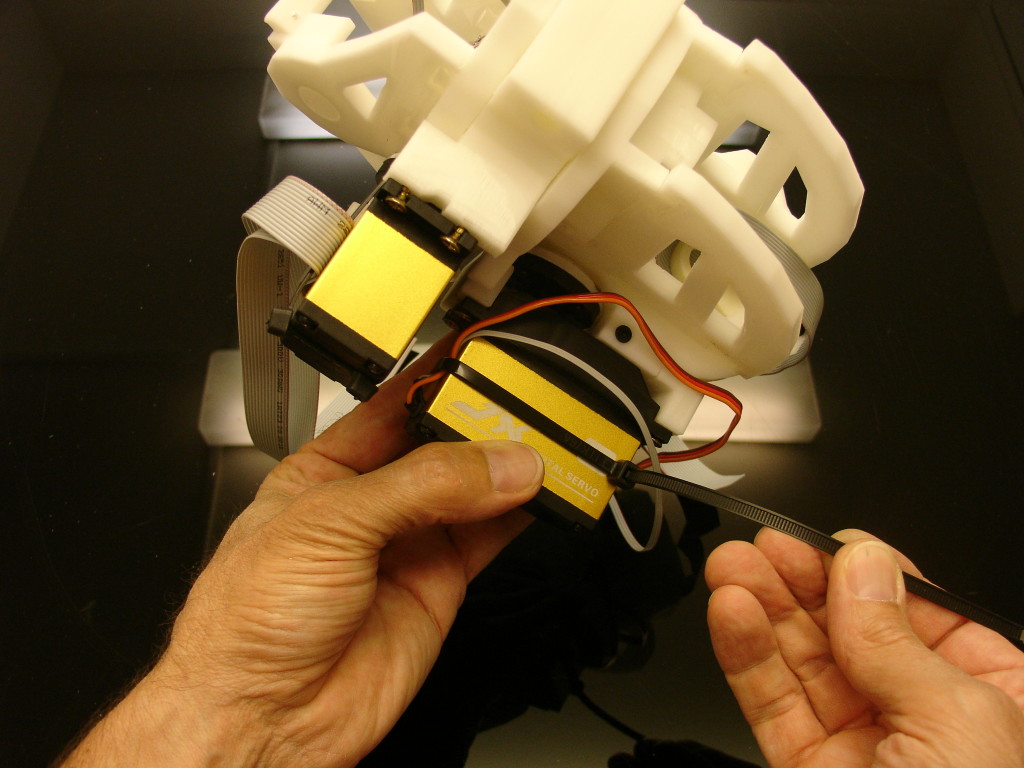
Add a zip tight (black) over the two cables coming out of the servo as shown. Cut the the extra length of the zip.
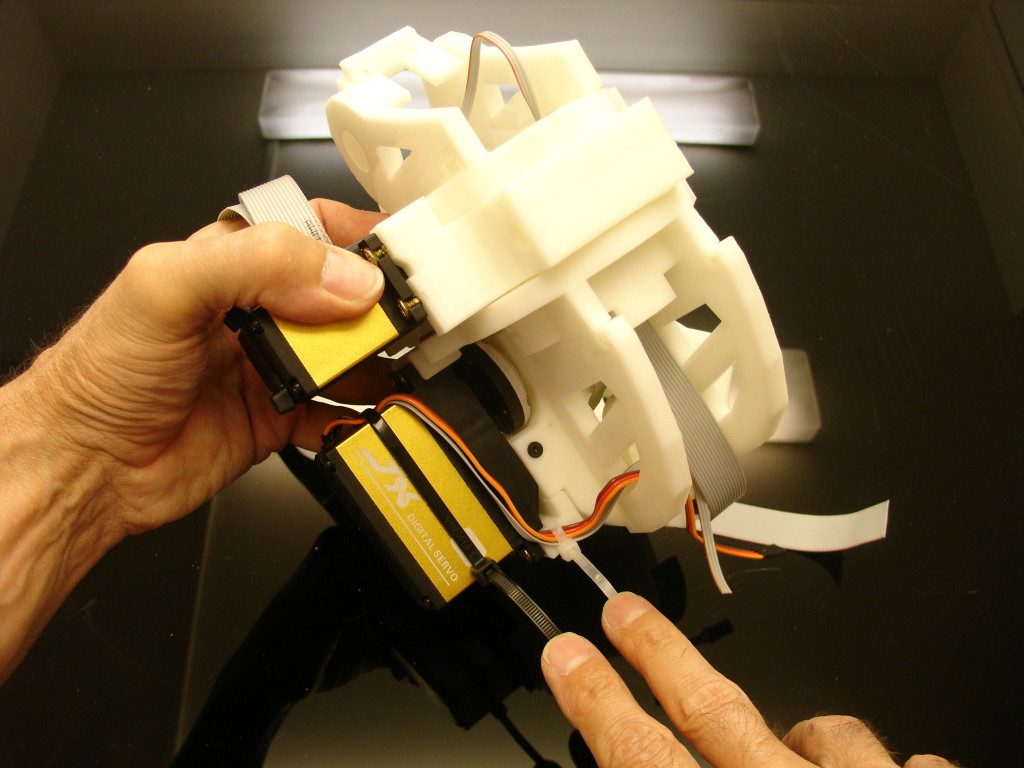
Put a second zip tight (white) to hold the cables and run them as shown through PivConnector. Cut the extra length of the zip.
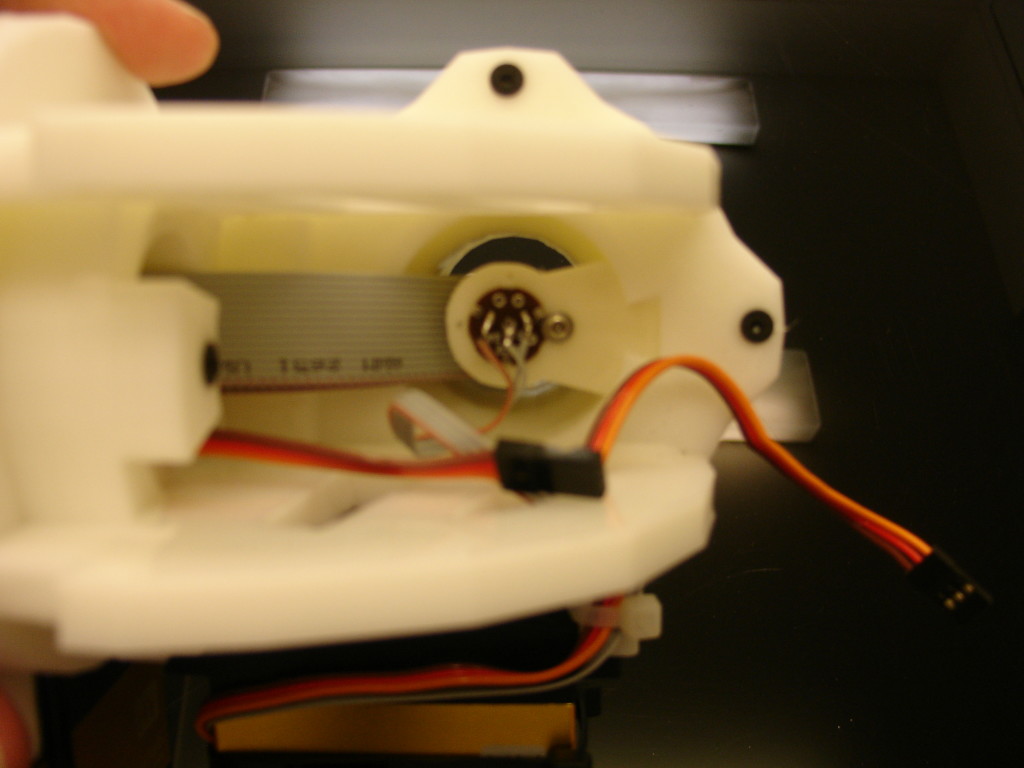
Add and solder the potentiometer. Make sure it is mounted as mine. Later you might need to adjust it’s rotation.
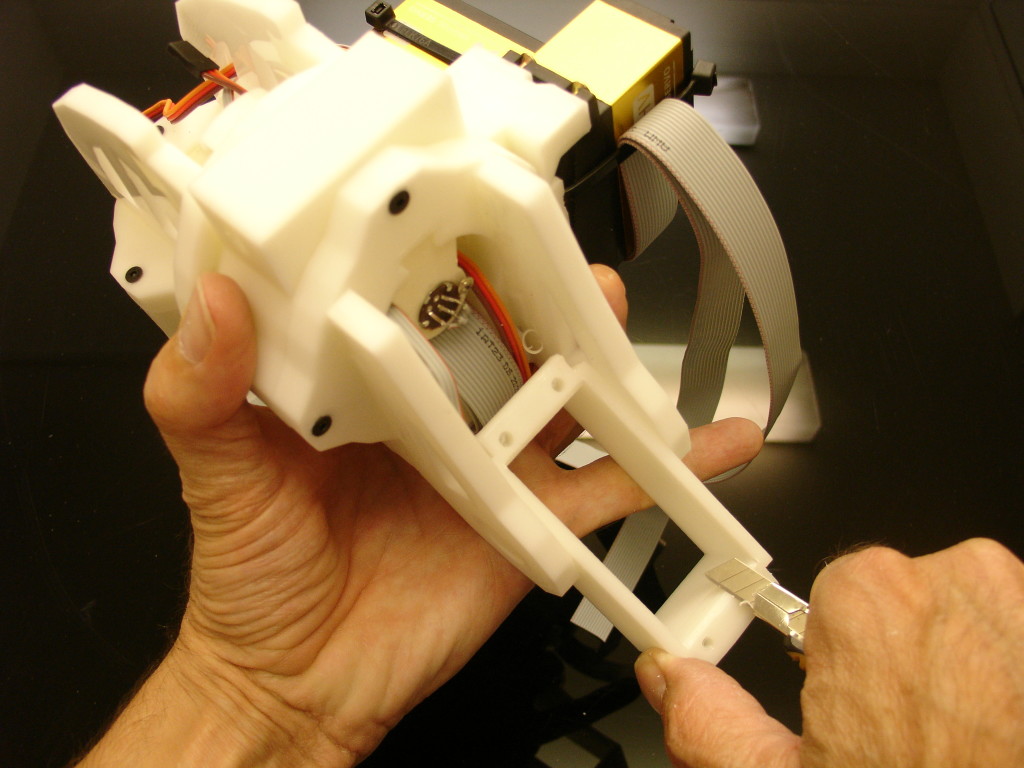
Trim the edge with a blade on ServoHolster, this will help to insert the servomotor. Depending on the model of servo motor, it can be a bit tough to push it in.
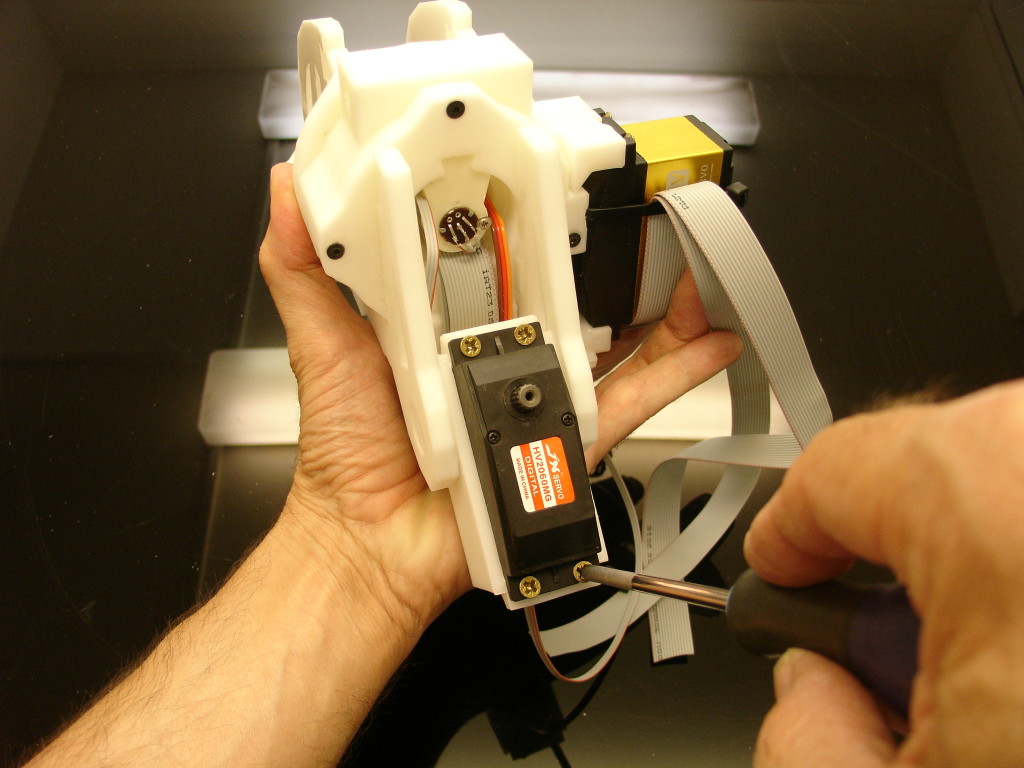
Add and tight the four standard wood screws 3.5mm x 16mm.
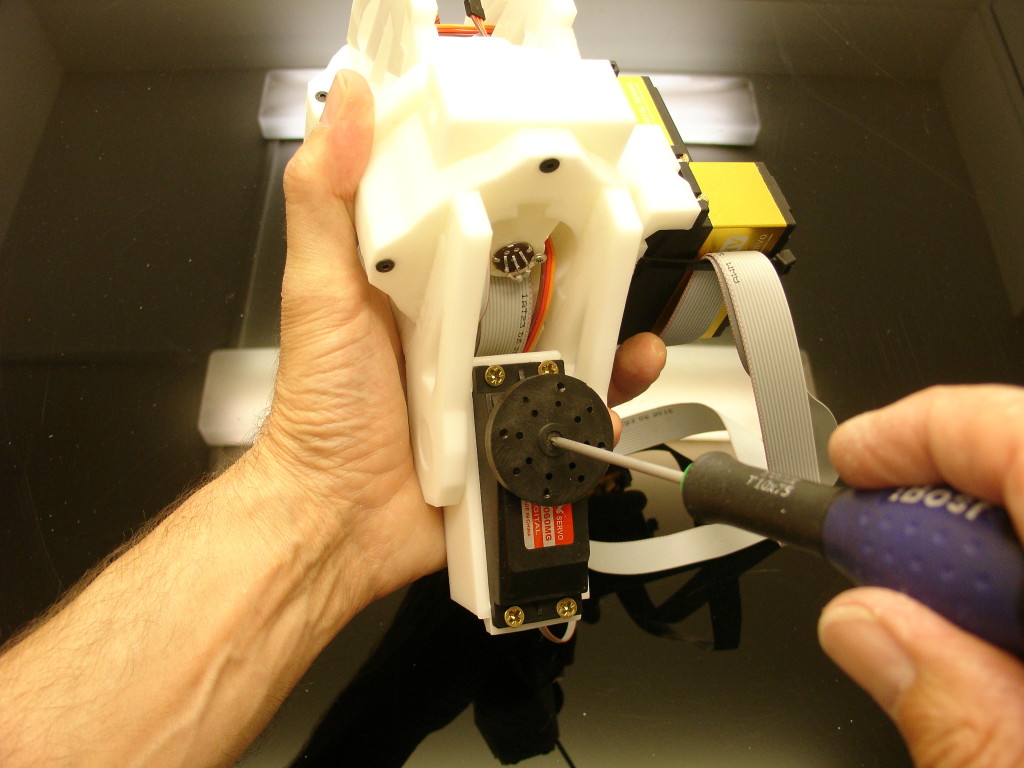
Mount the servo horn wheel to the servomotor and fix the 3mm screw delivered with your servo. Make this tight, this screw tends to loosen up with time.

Mount PistonClavi to the servo horn wheel. I use four hexagonal screws of 3mm, length 12mm, but you can also use some small wood screws.
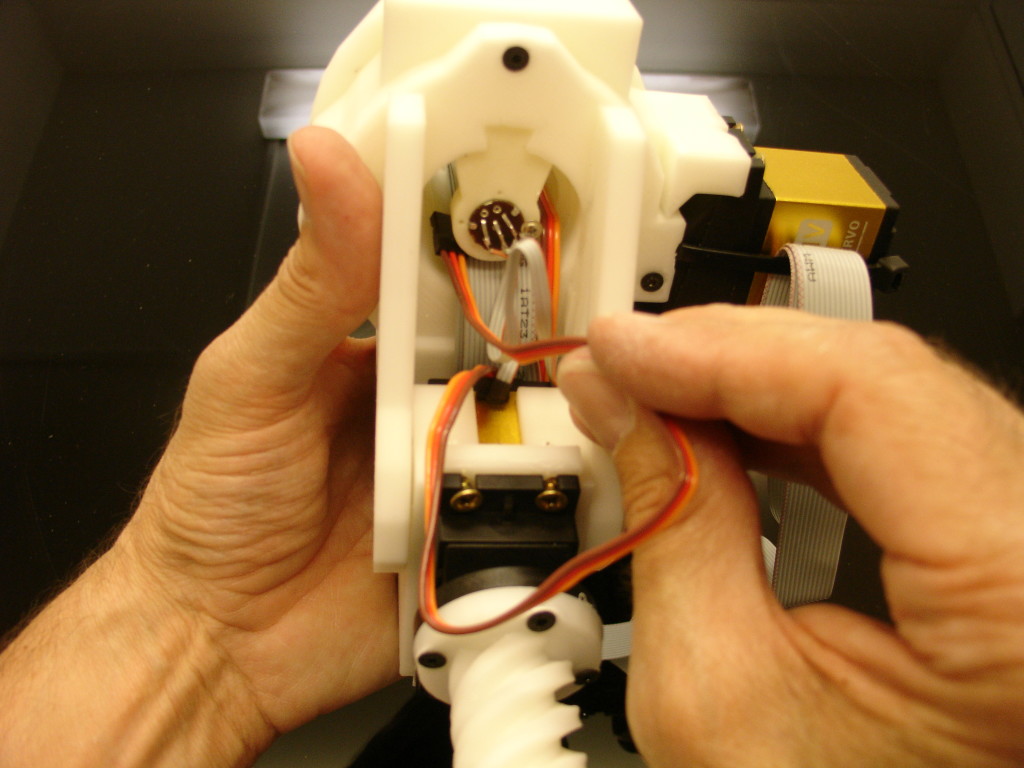
Run the servo cable into PivGear.
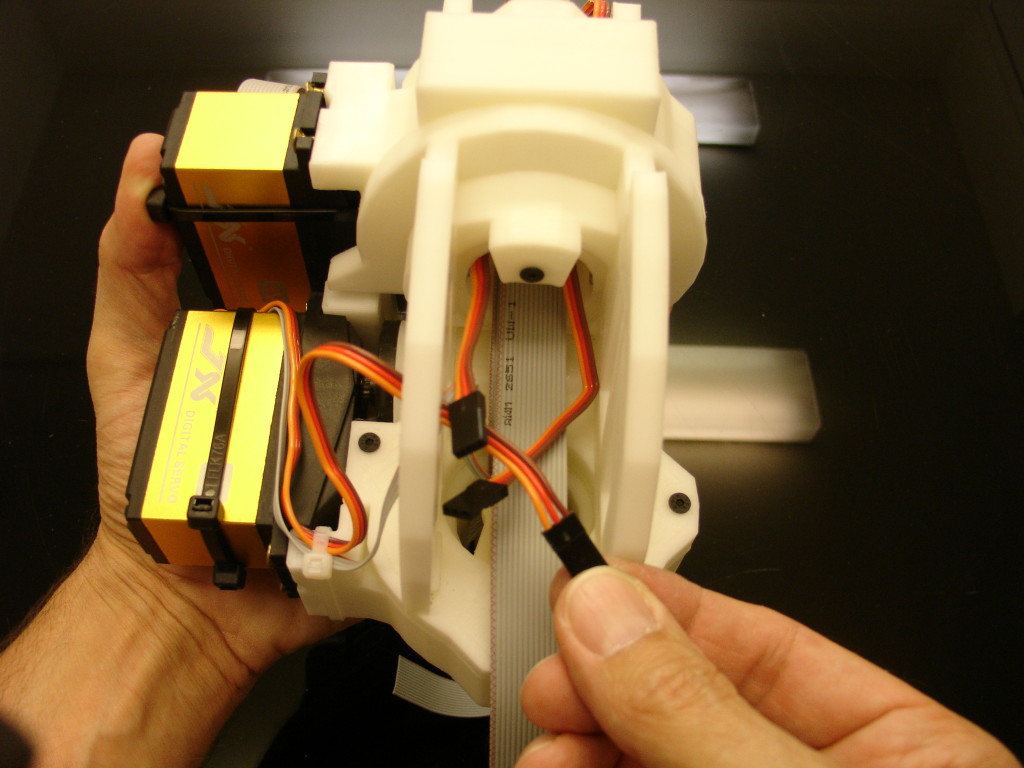
If all is right, you should now have the three servo cables connectors at the same spot.
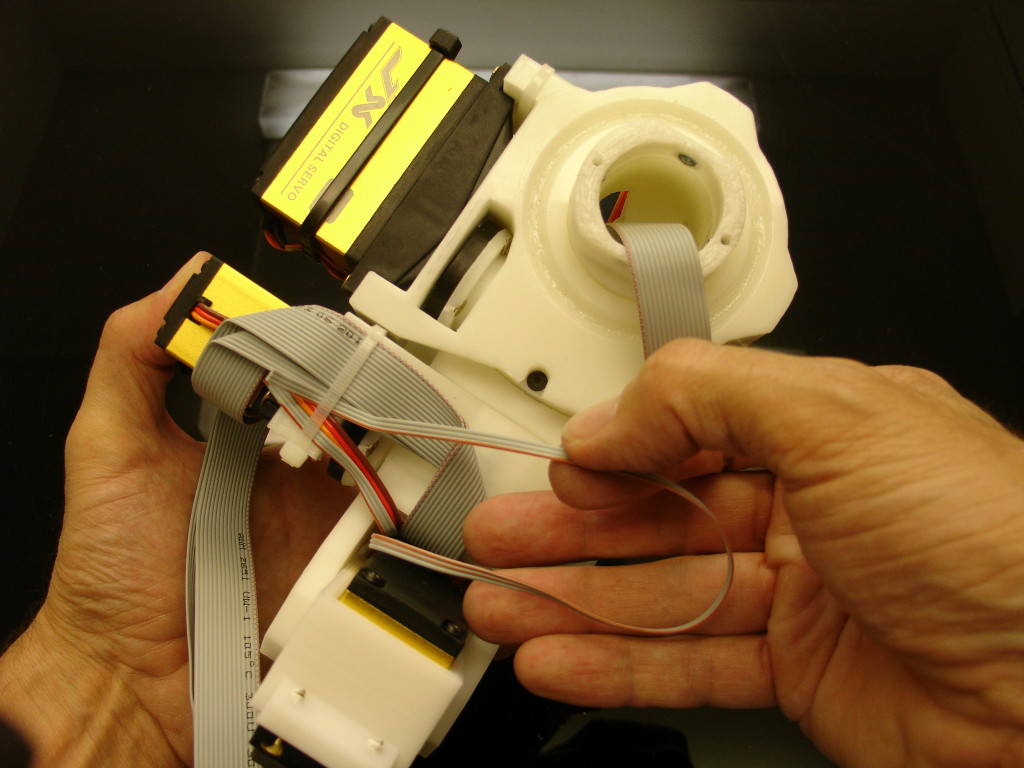
Run the third potentiometer cable through the zip tight(white) as shown.

Continue to run the third potentiometer cable through the second zip tight(black) as shown.
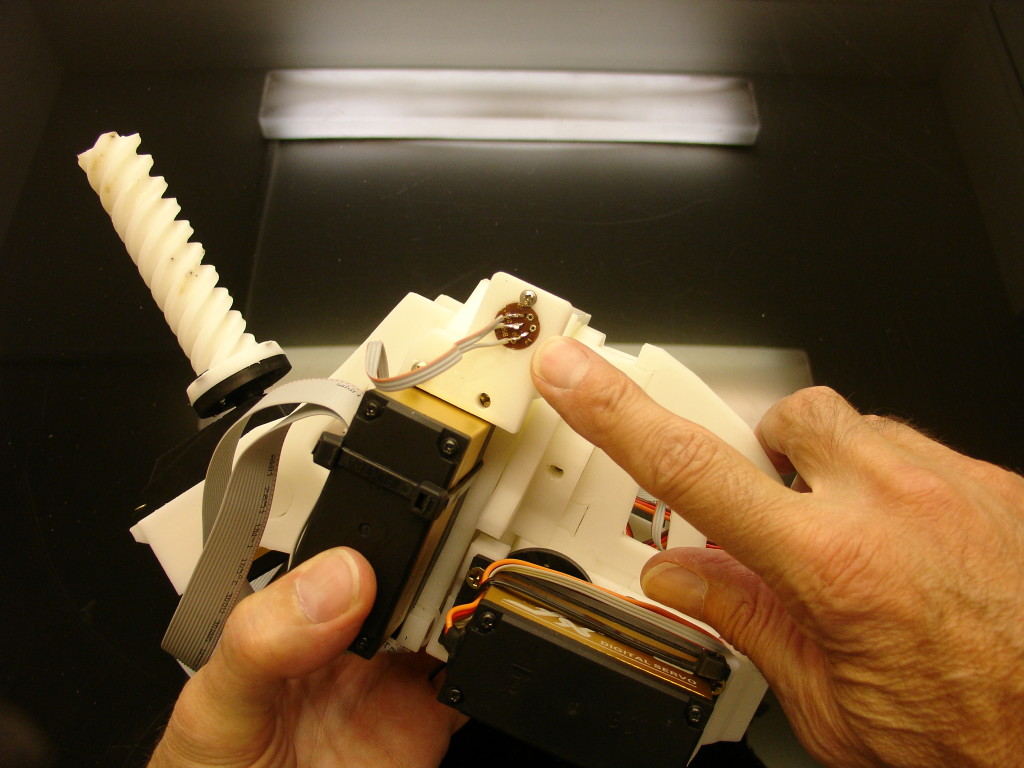
Place the PotHolder as shown, mount and solder the third potentiometer with a similar angle as in my picture. (Later, to fix the PotHolder we will need to remove two screws that hold the servomotor.)
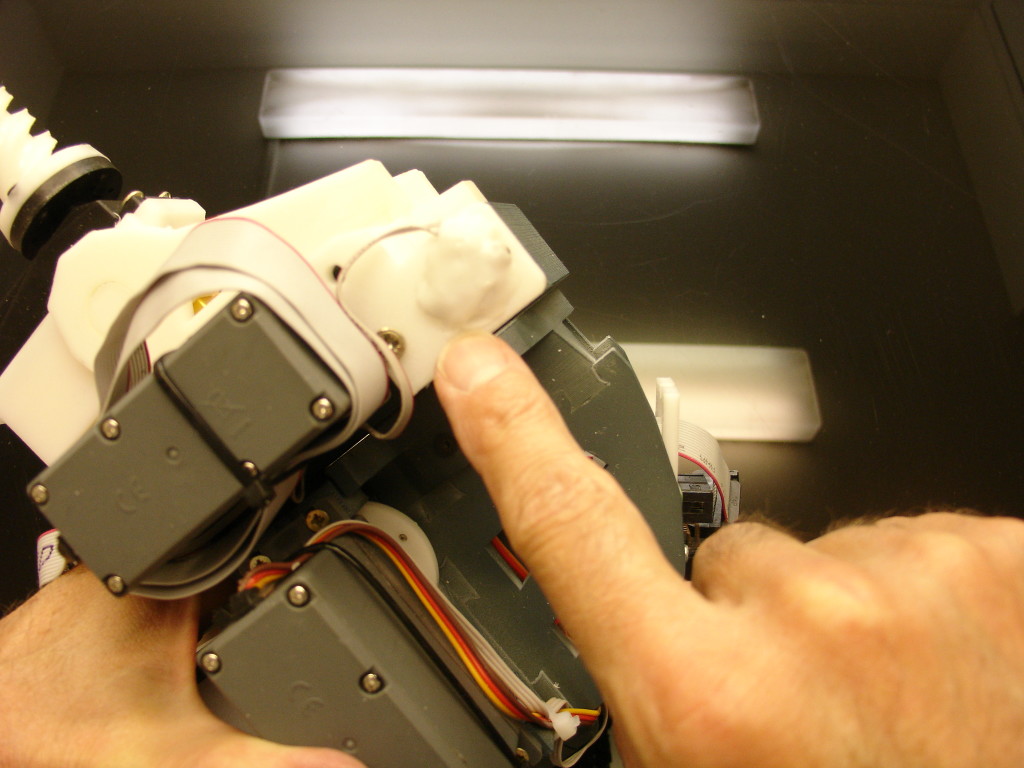
Also later when all potentiometers are well calibrated, it is good to protect the potentiometer solder with some hot glue(Hot glue Gun). But you will do that when you are sure everything is working well.
For info: if you want to remove hot glue, the best trick is to brush some alcohol on it, it will be easy to remove it.
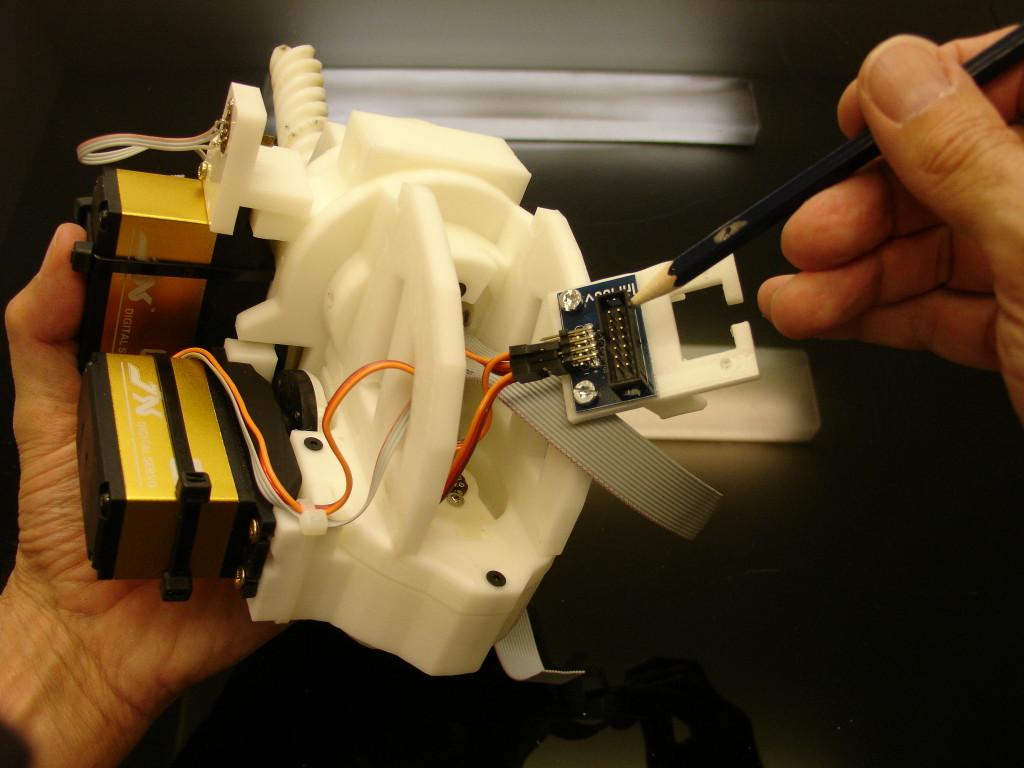
Screw the Arm breakout board to ShoulderConnect. And connect the three servo cables connectors to the respective pins (
see Hardware page & BOM)
-Omoplate pin 11
-Shoulder pin 10
-Rotate pin 9
-Bicep pin 8 (if you already have the bicep built)
Carefull to set the ribon very well seated in the headers as this can cause short circuits. (In this picture the header was doing short circuits and burned the ribbon.)

Plug the header to the Arm breakout board.
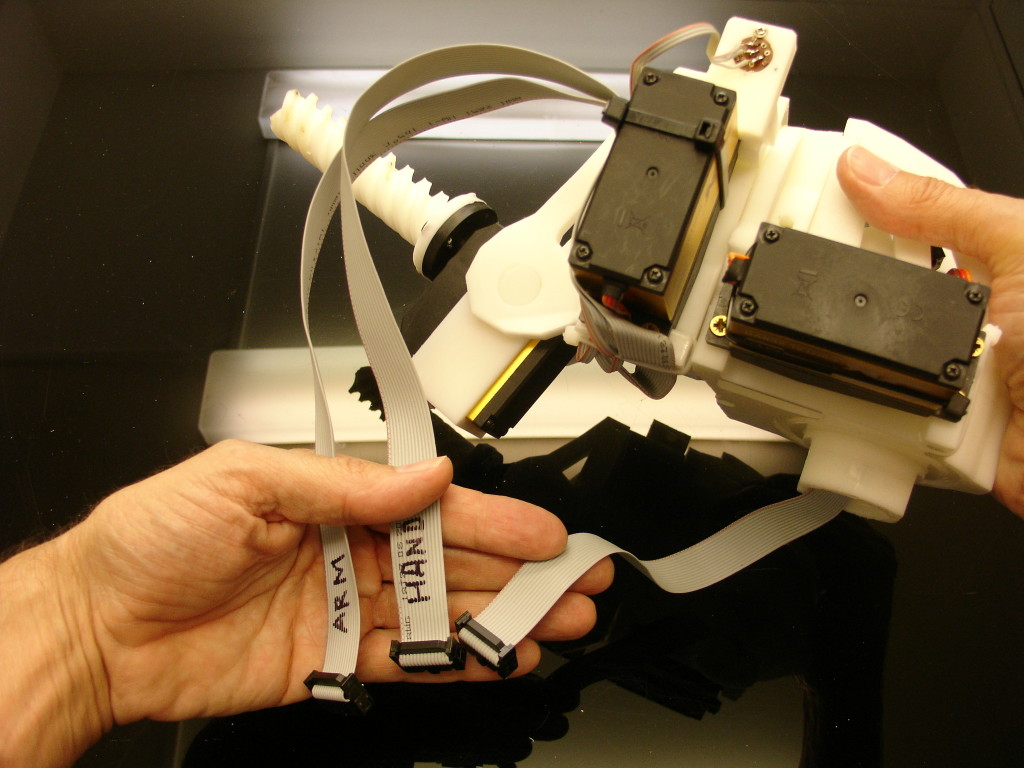
If everything is alright, you should now have something like this.

Add the two side screws 3mm, 20mm length. Do not overtight, you might break something.
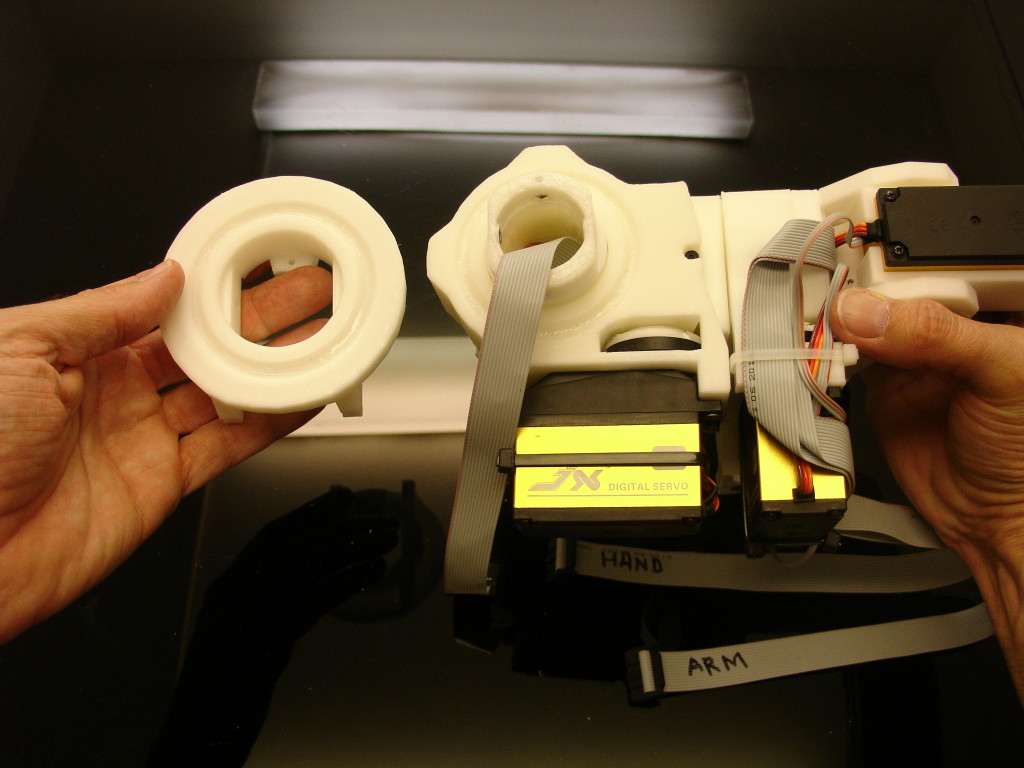
Lets get RotMit part ready.
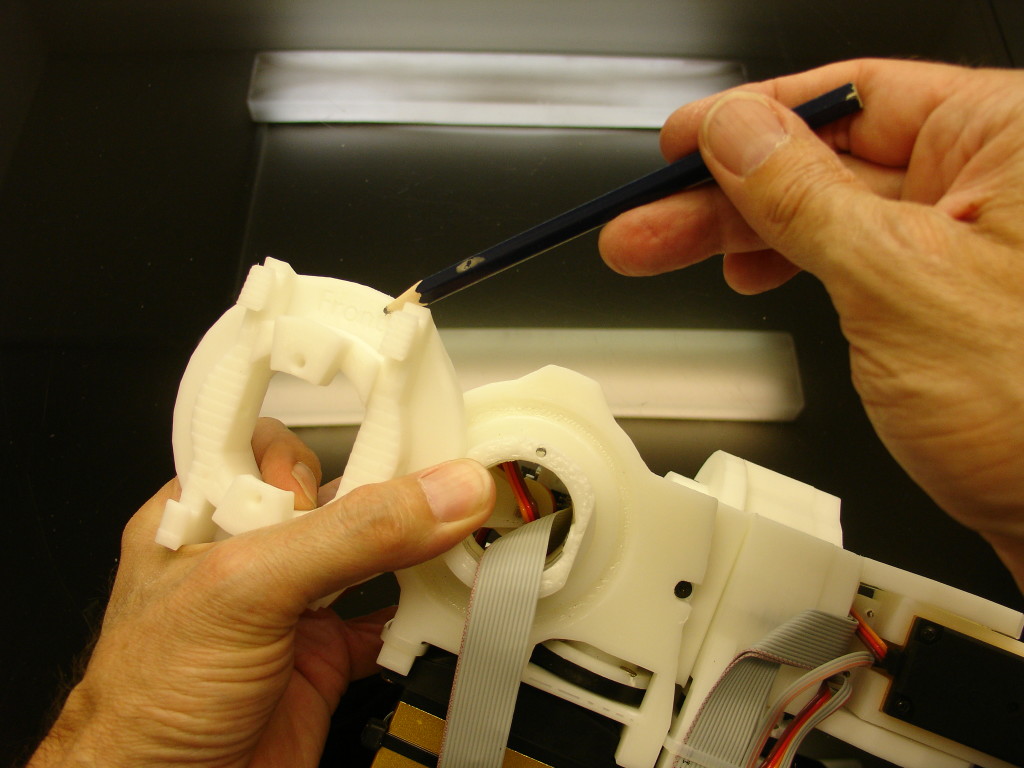
Note that it says FRONT on RotMit. This gives you the way it as to be assembled to RotGear.
Add grease and 31 balls.
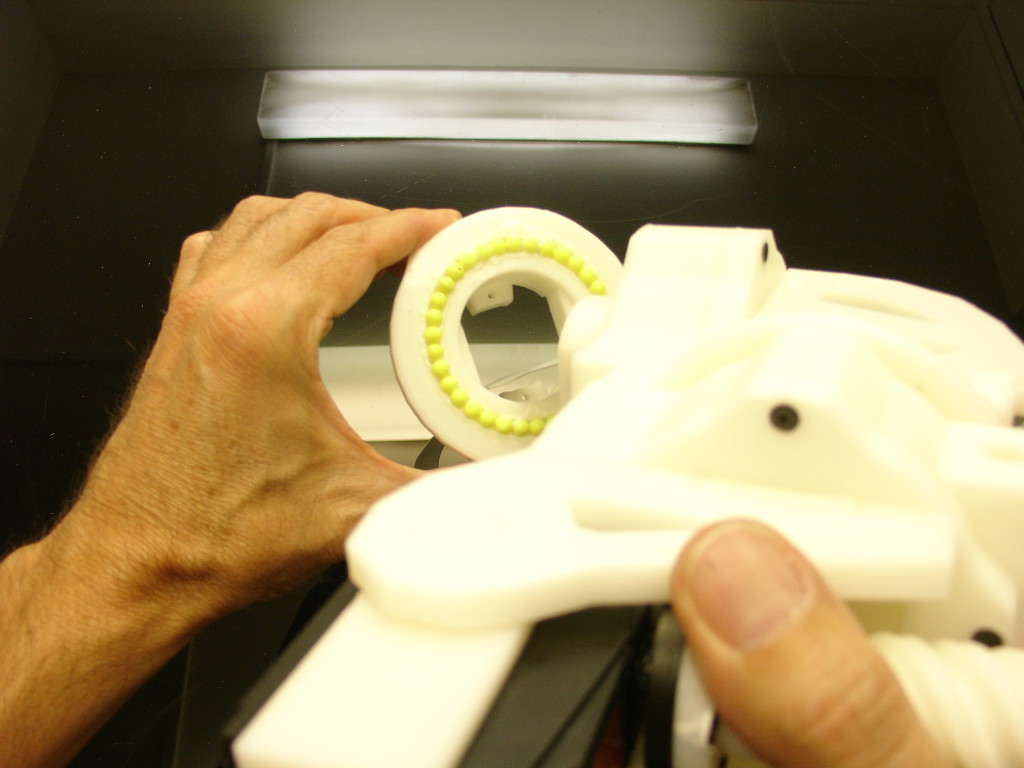
Assemble to RotGear.
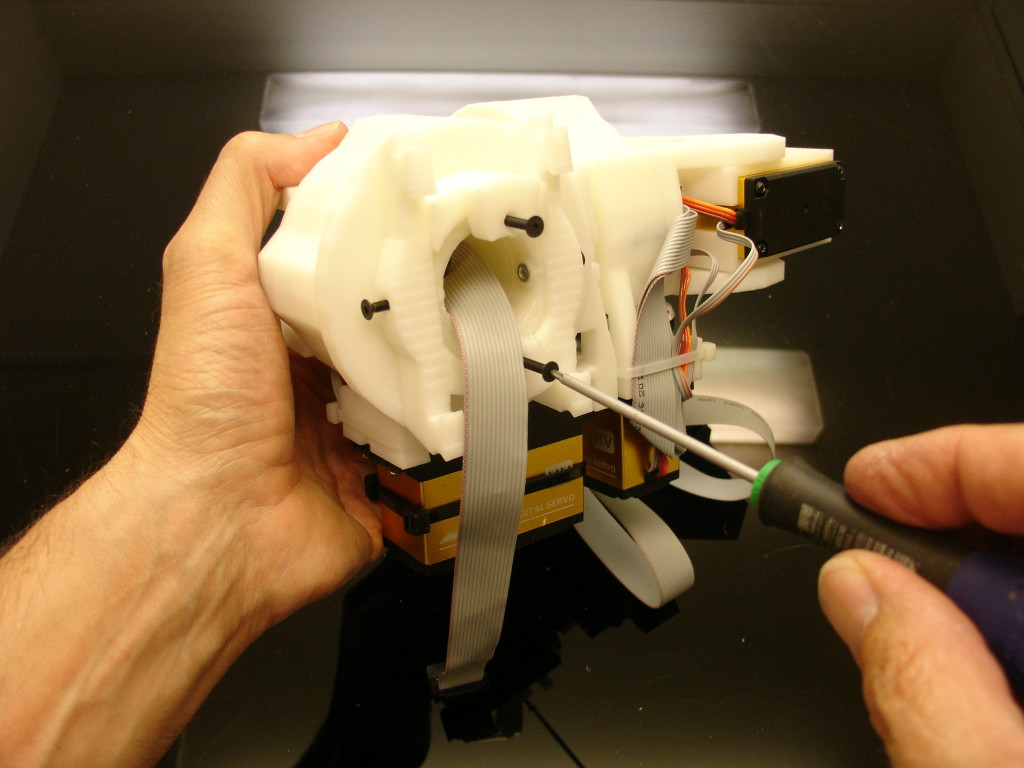
Add the two adjusting screws of 3mm screw of 30mm length. Do not over tight. These screws are only meant to adjust the pressure on the ball bearing.
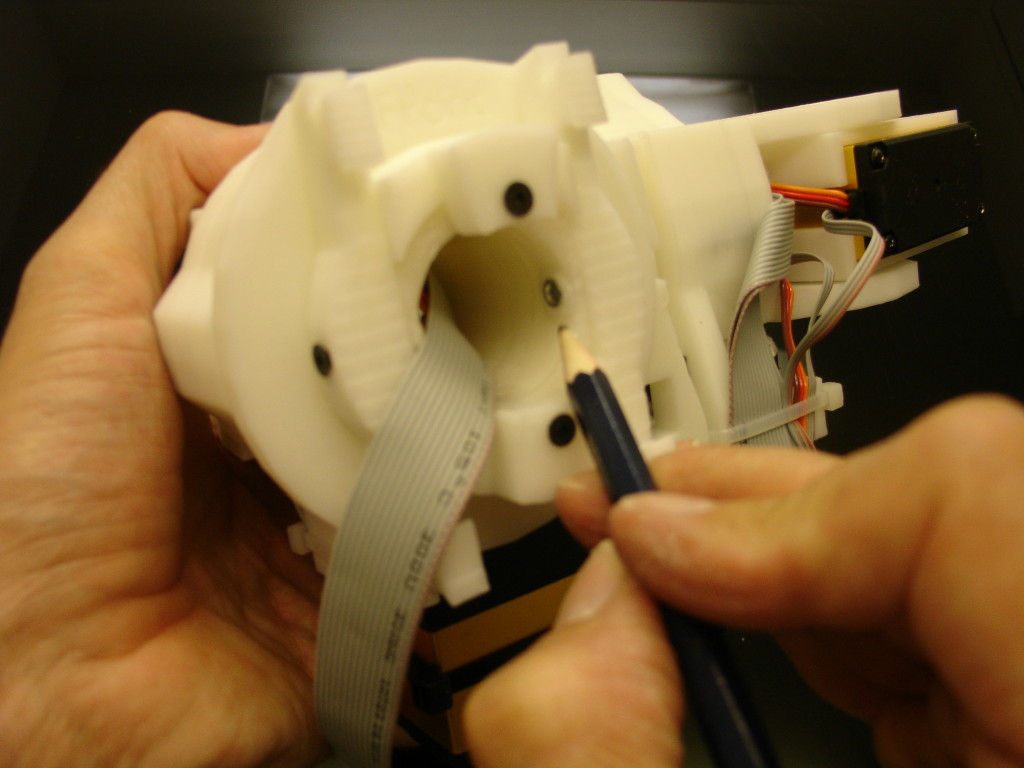
Add and screw the two side screws of 3mm, length 20mm. Make sure they are not longer to the inside. It is important otherwise it might damage the Piston of the bicep.

Insert RibbonPusher.
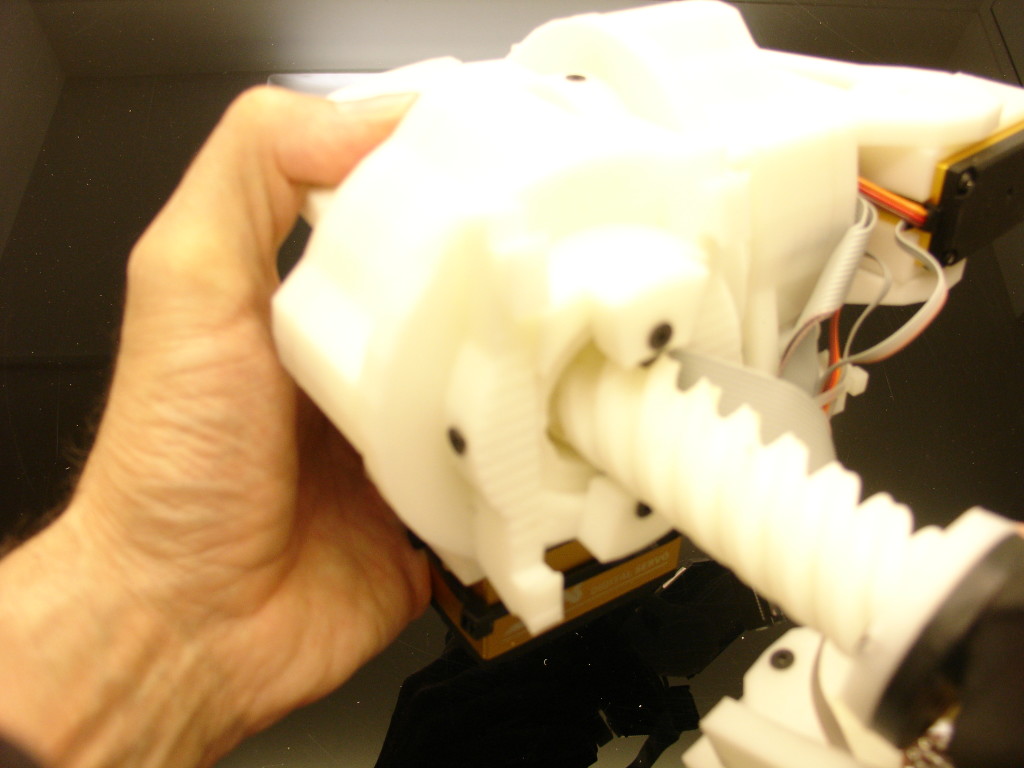
As you see, this is only to hold the ribbon cable to avoid friction against the Piston of the bicep.

Assemble the shoulder to Clavi parts with a 8mm, 90mm length screw. (Don’t mind the ribbon cable, it’s a older version picture)
Attach the bicep parts to the shoulder parts if you have them ready.
In the back of the shoulder clip the first part of “PivPotHolder” to “ClaviBack”.
In your case PivPotHolder has a nut shell for 8 mm nut. (On the picture above it’s a older model)
Remove the two screws attaching the servo and put in place the second part of “PivPotHolder”.
Use longer screws to go through the servo holes.
Connect the two ribbons to your NervoBoards respectively on Arm and Hand.
You are now set to GO for your first test. One thing you should keep in mind is that the servo actuating “PistonClavi” should stay between 0 and 80 position, if you go further it will certainly break. Now if you use InMoov service from Myrobotlab, this is already implemented to avoid breakage. Remember to do your test in a large space, and check your wires so they don’t get torn off.
Tip for testing: Personnaly, I test servo by servo each position before launching the whole shoulder. To do that I just unplug the servo cables that I don’t want to power on the Arm minibreakout board.
STEP 4:
Setting up the shoulder to default position.
Script to learn how to use MyRobotLab with the Arm and shoulder.
Setting “omoplate” servo and potentiometer to default “Rest” position 10 on a range from 0 to 180
To reach this value you may have to rotate slightly your potentiometer in it’s bracket.
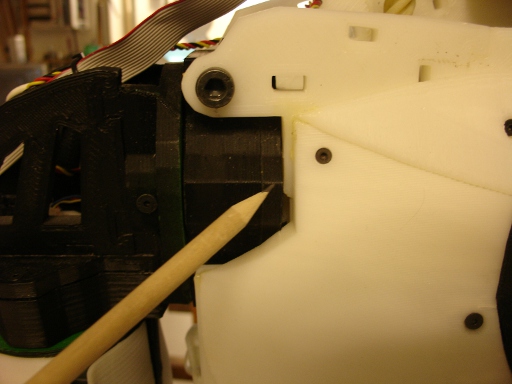
When omoplate is at default 10 position there is no gap between these two parts

See video for the omoplate movement:
https://inmoov.fr/wp-content/uploads/2015/10/MOV05330.mpg
##############################################################################
Setting “shoulder” servo and potentiometer to position 33 on a range of 0 to 180. It is not the default position for “rest” but this way, we can align the two servos seen from the back of InMoov.
To reach this value you may have to rotate slightly your potentiometer in it’s bracket.
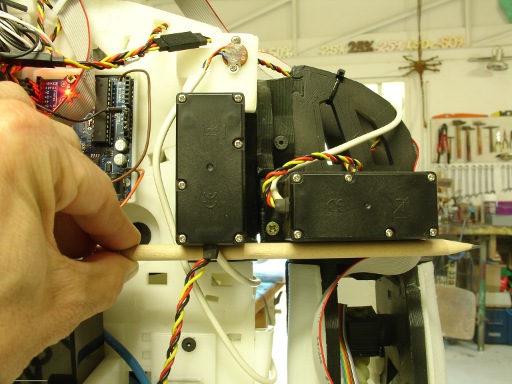
See video for the shoulder movement:
https://inmoov.fr/wp-content/uploads/2015/10/MOV05329.mpg
##############################################################################
Setting “rotate” servo and potentiometer to default “Rest” position 90 on a range of 0 to 180.
Align the parts as shown on the pictures.
To reach this value you may have to rotate slightly your potentiometer in it’s bracket.
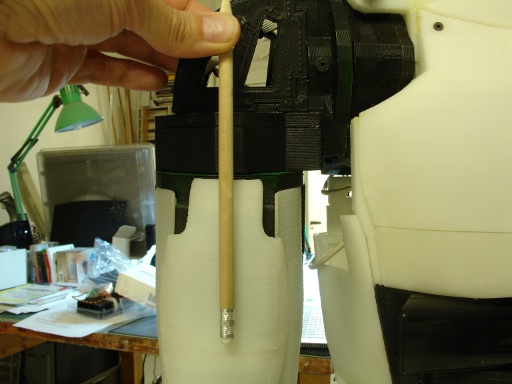
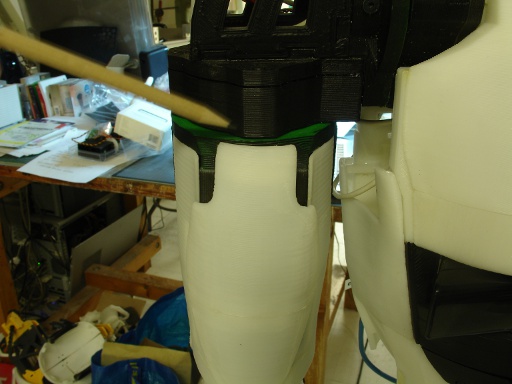
See video of the “rotate” servo movement:
https://inmoov.fr/wp-content/uploads/2015/10/MOV05328.mpg
OLDER TUTORIAL:
Assemble “PivGear” to “PivCenter”
It should turn in it smoothly but without backlash.
Using a fear amount of grease is a good idea.

Ok, This section with green parts is the same than for the bicep so I re-used the pictures and changed the name of the parts. This picture is to show you what is the angle position of “PivCenterV1” compared to “PivMitV1”. Check the little rectangle hole where the potentiometer will go.

So keeping the same rotation angle, mount “PivmitV1” to “PivgearV1”.

I used clamps to make sure there wouldn’t be slack between all three parts during pre-screwing. Leave them like this, we will screw them definitly together in a further step.

Attach one servo to “PivcenterV1”. For to do so: mount but don’t tight fit the white actuator wheel.

Once the servo is attached, you can tight the screw.
Clean up the support on “PivWormV1”

Mount “PivWormV1” to the actuator with 4 little screws, make sure they don’t come out behind the actuator, otherwise you have to cut them. I made it operate a few turns by plugging the servo on the Arduino. Then I cleaned up the dust created by the parts.

Before closing the case with “PivTitV1”, make sure you used a good amount of grease, every where on the gears. (sorry the servo is not mounted on this picture)
Mount the two “ConnectorV1” to “RotTitV1” and “PivMitV1”, making the junction between the bicep and the shoulder.
Glue with acetone all three parts together, and do it well, this is going to take a lot of pressure.
This is how they should be positionned. (sorry this picture is after everything is built)
Set “PivGearV1” in this rotation angle to “PivMitV1”. Here have a close look at angle of the hole of the potentiometer inside “PivGearV1”. (sorry the screws of the next step are already mounted on this picture)
Use a longer screw to assemble “PivGearV1” to “PivMitV1” to “RotTitV1”
Use a clamp to make sure there is no slack between the parts during mounting.
Then screw “PivGearV1” to “PivMitV1” on the sides and top.
Put together the two “ServoHolderV1” and “ServoHolsterV1”
Mount the assembly to “PivTitV1”. Glue well with acetone, this is going to take pressure too, but make sure the “ServoHolsterV1” can rotate freely.
Set in the potentiometer into “PivPotentioV2” and clip it as is.
Here make sure the welding for the right shoulder. Red wire being on top, yellow in the middle, and blue on the bottom. I used hot glue on the weldings to avoid short circuits.
Mount with screws”PistonClaviV2″ to the white wheel of your servo. set your servo into “ServoHolsterV1” with screws.
Attach the complete arm to the shoulder parts.
In the back of the shoulder clip the first part of “PivPotHolderV2” to “ClaviBackV1”
Remove the two screws attaching the servo and put in place the second part of “PivPotHolderV2”.
Use long screws to go through the servo holes. Fix the potentiometer in place as is.
You can see on this picture I used “arduinosupport” from
the hand to set my Board.
Fix the bolt to complete the attachement of thearm to the shoulder.
Connect the two ribbons to your NervoBoards respectively on Arm and Hand.
You are now set to GO for your first test. One thing you should keep in mind is that the servo actuating “PistonClavi” should stay between 0 and 80 position, if you go further it will certainly break. Now if you use InMoov service from Myrobotlab, this is already implemented to avoid breakage. Remember to do your test in a large space, and check your wires so they don’t get torn off.
Tip for testing: Personnaly, I test servo by servo each position before launching the whole shoulder. To do that I just unplug the servo cables that I don’t want to power on the Arm minibreakout board.
Go to STEP4 for to set up your default positions.
rotate the potentimeter is unfortunately only possible if you have round ones, the newer HS805bb+ has rectangular potentiometers
Mmmmh, yes that might a problem. Did you use the rectangular pot holder from Thingiverse? I don’t have rectangular pots, other wise what shoud be done is to modify the file to make sure the pot is correctly positionned once mounted. But it will imply creating a left and a right pot holder.
hola Gael sabes como se puede saber de cual es la posición que deben tener los potenciómetros ?
in omoplate and biceps i have the round poti but when i ordert the next servos i have got the newer version with the rectangular poti
and so i do it just with a dremel and glue the potentiometer with hot glue but that was not the best solution.
i think about to create a holder with only the round hole for the poti so that you can rotate the poti in right position and a second part like a clamp wich is screwed and holding then the poti in right position
Square pot holder:
http://www.thingiverse.com/thing:533469
http://www.thingiverse.com/thing:254664
hello Gael, now i have a better solution for all, it is possible to buy the round potentiometer for the servos seperate. i found it as a examble in a german shop
http://www.modellsport3000.de/cosmoshop/cgi-bin/lshop.cgi?action=showdetail&artnum=3-8120
its not cheap but so there is nothing to change on the design
greetings tom
Yes that is an option, They are a bit expensive though…
Did you try making it with the rectangular potentiometer? Because i too have the new servos…
Hi David, I haven’t personnaly tried with a rectangular pot but you can find modified parts that might suit your needs.
http://www.thingiverse.com/hairygael/collections/inmoov-parts-and-derivatives
Hi, wanted to ask, ThroatHole that is available to print now is a bit different from the one on here, how is the new ThroatHole attached the sticks that are attached to the HomePlate Back are longer then the ones on the previos should they be sticking out or?
I can’t find the ServoHolsterV1 that is in the tuto, the new ServoHolsterV1 is has no attachments like the one on the picture
Dear Gael
I´m been working the shoulder and the biceps of the InMoov. I´m using other servos, the CYS-S8218 Digital 6V-7.2V Metal Gear 40KG Torque Servo. Because they a smaller than those you recommended, I had to modify lots of pieces to adapt to the project. Although the hardworking I have to confess I´m having progress and lots of fun.
Sincerely
Cesario
Hello Gael!
Where it is used ChestTopAttachV1.stl ?
The photo is desirable.
Hi,
It is attached to behind ChestTopV1 to be fixed to the torso structure.
bonjour a tous je voudrais savoir si tout les pièces du torse ,de l estomac , etc… son coller ou pas ?
ou simplement emboîter
merci .
Bonjour Dany, You should post your questions on the forum, it would be better. (forum)
Les pièces du torse et estomac sont emboitées. Suivant votre qualité d’impression, celles-ci tiendront bien ensemble ou peut-être pas, dans ce cas il vaut mieux faire des points de collage aux endroits qui vous paraissent stratégique. Pensez démontage car peut-être aurez vous envie d’installer des updates par la suite. Donc évitez de tout coller inutilement.
ThroatLowerV1 is not in the parts list. Help!
You need to look a little better
http://inmoov.fr/inmoov-stl-parts-viewer/?bodyparts=Torso
Surely Saurabh Sikka, meant that the ThroatLowerV1 part is not present in the beginning list of this page, in fact it would be right to describe that they are two pieces.
Congratulations on the project.
Just wondering if anyone has developed a female torso..or would that take too much plastic
athough it would add more space for my boards
I love the idea
Hello Gael, Can I use Servo Tower Pro MG945 ?
info about it : http://www.servodatabase.com/servo/towerpro/mg945
Hello,
You need to find the size specifications and compare them with the recommended servos. But I’m guessing the MG945 will fit because the MG946 does.
hi i cant able to fix with mg946 so kindly give me any solutions for the same awaiting for your answer
Hello, your prints must be a bit too small maybe? You may need to re-calibrate your printer.
Hello, i am trying to make the shoulder but the parts you are using and the parts that i downloaded are different
i am very confused now please help thanks
SIncerely Gabriel
Hello,
Tutorial pictures for the shoulder are based on my first design. I have modified them over the years, but they remain pretty much the same. Unfortunately I didn’t re print my latest updates and therefore haven’t been able to update the tutorials. If you have doubts, you can always post your questions on the forum for help.
HS-805BB This servo is so costly can i use any cheap servo alternate of this if yes then please provide me the link of that
In trying to get the pot out of my Hitec HS-805BB servo I found the motor glued in very firmly. I desoldered the 3 pads holding the PC board to the motor then the PC board come right out with easy access to the pot
Hello,
Yes it is another method which can be used as well.
Here is another solution posted by an InMoov builder, if you can’t open up your servo the way I did it, of course if you have a solder pump, it will be even easier:
https://youtu.be/4ia6zoRKujI
Or this video:
https://youtu.be/BM4oDbYcKwo
Or you can also watch these videos posted by a InMoov builder:
http://youtu.be/EwebQTuTAcw
http://youtu.be/5usFR3W61SA
http://youtu.be/5-nxuoqT8Ho
http://youtu.be/J8Q-bUT-IJ0
http://youtu.be/t1LBbmfRvOQ
Here is another set of videos, in which the technique involved is to remove the solder on the three motor connections, leaving the motor in place instead of romoving it:
Video-Tuto-Pot-Servo.rar
Hi Gael,
I am now printing parts for the shoulder assembly. I found schematic on the parts fit together. However from the list of parts, I am unable to locate a schematic assembly for the remainder of the parts:
-clavibackv2
-clavifrontv2
-leftpivpotholderv2
-pistonbasev6
-pistonclaviv3
-pivcenterv1
-pivmitv1
-pivpotentiov2
-pivpotholderv2
-pivtitv1
Is there an exploded diagram that shows the assembly for the remaining parts?
Hello,
Diagrams are here:
http://inmoov.fr/bicep-assembly-3d-views/
http://inmoov.fr/shoulder-torso-and-chest-assembly-3d-view/
Where does the “leftpivpotholderv2, pistonbasev6, pistonclaviv3, pivpotentiov2” get connected? I don’t see these anywhere on diagrams.
where i find the HomPlatback+V1, ThroatHoleV2, HomPlatback-V1, ThroatHoleV2 project?
All parts and STL are in the gallery:
http://inmoov.fr/inmoov-stl-parts-viewer/?bodyparts=Neck
http://inmoov.fr/inmoov-stl-parts-viewer/?bodyparts=Torso
i’m very sorry, but i can’t find the ThroatHoleV2 prodject.
i’m very sorry, but i can’t find the ThroatHoleV2 prodject.
Hi Gaël, thank you for the new shoulder and bicep parts, am printing the new parts right now, and going to put them on my V2 inmoov. Hopefully i will have them ready before the end of december, because as you know ill be out for surgery then. My planning is to have the fully printed and working inmoov ready for the luxembourg maker faire!
Again it was nice to see you in eindhoven and also give anneke a big hug from me, and hopefully see you soon again, with my inmoov standing proud next to yours!
Wow, great that you are adding the new shoulder version to your InMoov V2!!
I sure hope you can finish before december and I will be waiting to see you at the Luxembourg MF!
Be safe and I give you all my thoughts regarding your surgery.
how would i build the left shoulder
Follow the tutorial for the right shoulder, just mirror mentally…
Hi Gael,
Could you tell me what kind of cable tape you used? Or how can I select it? From what I understand, this cable must withstand the current of the servos, then it must have an AWG standard or minimum width to withstand the current?
Regards
Hello,
I used standard Ribbon Cable 14 Conductor 28 AWG Flat Cables.
Hi
I have just finished printing the front and back torso structure.
I would like to hold it together tighter with bolts, as I realize that I am not meant to glue front, inside support and back together.
Is there good spots on the front and back structures to do this or will there be problems due to the infill of the individual parts.
It seems as though the front and back are not going to hold together strongly.
Kind Regards
Ian
Personally, I glue the parts together in a few spots. When InMoov gets transported in airplane, the vibrations can slowly take things apart.
Hi, could someone help me please, im loocking for the parts that are for the RIGHT shoulder.
when i go on the gallery section i put for shoulder parts and there are only parts for the left side.
thanks
i just realized they are under another name, sorry
No problem.

1x ClaviBack
1x ClaviFront
1x PistonClavi (if you have a trouble fitting this part with pistonbase, you can decrease the X and Y size before printing of 0.1 or 0.2mm)
1x Pistonbase
2x PivConnector
1x PivGear
1x PivMit (add support)
2x PivPotentioRound or PivPotentioSquare
1x PivPotholder
1x PivTit (add support)
1x PivWorm
1x Pivcenter
1x servoHolster (add support)
1x servoholder
1x shoulderconnect
shoulderconnect I cant find this
This is one of the 3 only STL parts which are for sale on the shop page.
So I only need these parts with these quantities to print the whole shoulder?
Or do I need to print the whole list twice?
Hi is the RibbonPusher an STL or something else? I can’t seem to find it in the BOM or STL library, thanks-James
http://inmoov.fr/inmoov-stl-3d/?bodyparts=Bicep&parts=RibonPusherV1.stl
It helps to maintain the ribbon cable applied to the extern wall inside RotGear while the piston of the bicep goes up or down.
Hi Gael
I am trying to figure out how the servos work being continuous rotation, I did the hake following your directions, when I center the pot, the servo stops, but as soon as I send an instructions to go for example 180 the servo continues to run without stopping, I am testing with an arduino. I have my robot half way, when I star testing the elbows and shoulder, i notice the servo does not stop unless i bring it to the center, I am using the calibration servos tool.
I really appreciate your help.
Best
I don’t know which servo you are using, but some servo have a inverse rotation.
Try to reverse the polarity on your potentiometer, I suspect that could be your issue.
Hi Rafael,
Gael hat recht. Genau das Problem hatte ich auch. Du musst die beiden äußeren Pole am Poti tauschen, dann sollte es klappen.
Gruß Andy
Sorry I forgot to mention that, I am using HS-805BB, I have some with the polarity reverse according your tutorial, but they all behave the same, what I don’t understand is how the servo can stop at let say 180 degrees with the continuous rotation.
Thanks.
What determines the angle position of the servo is the potentiometer. When the motor turns (even if it is continuous) the potentiometer TURNS ALSO and gives the feedback of it’s angle position to the controller.
If the potentiometer polarity is inverted, the motor will increase it’s rotation instead of stopping when the potentiometer reaches the desired position.This is not what we want because it damages the potentiometer.
I hope this helps.
Gael, I really appreciate you taking the time to answer my questions, I think the problem come from my confusion in the tutorial when you mention the wires should be inverted depending if the right or left , what I did invert was the the plus and minus wires of the potentiometer, I think I undrstand now ( I hope) that I should change the signal and the minus wire.
Gael
I want let you know that the latest version zip file is corrupted, when you download and try to decompress got error “files is invalid”, the older versions are ok.
Hi Gael
Rebuilding Borne’s shoulders and realized I didn’t have lower arm for square pot. Can you please tell me where it might be.
Thanks so much for your vision
Scott
Hello,
I didn’t redesign this part for square potentiometer. However you will find it available here:
https://www.thingiverse.com/thing:533469
Hello Gael, I was wondering if it is possible that there is some lost file. It seems that I can not find the ThroatHole file. Can you provide the file?
Thank you
Can we use acrylic sheet laser cutted part for Torso and back instead of 3d printing?
Yes you can.
good day. With that servo I can replace the model HS-805BB, because in amazon there is no more that model and it is the only place where I can buy. Thank you
saludos estoy armando los hombros del inmoov pero no encuentro las piezas del hombro derecho si alguien podria ayudarme de ante mano muchas gracia.
Hello,
All parts are in the galery/STL_library.
https://inmoov.fr/inmoov-stl-parts-viewer/?bodyparts=Shoulder
I am building the right shoulder but I am blocked in step 3 since I can not find the piece named “Soulder Connect” to which I should screw the Arm breakout board. Can anyone help me?
Solved. I have realised that the piece is not available for free it is in the Inmoov shop.
Hello Gael, I want to design and print a piece to be able to hold the immov’s high part, would you be so kind to send me the measurements or the design of the kineckmitback and kinectmitfront pieces? I want to design a piece to attach it to a solidary tube with some wheels. Thank you.
Hey I’ve got a question. Do you still need to print the homplate files, which you can find in the STL gallery? Ore are those no longer needed?
Hello, yes you still need to print those parts
I looked and couldn’t find the dimensions for the round potentiometer so I looked at the round part for a pot and measured 3 dimensions. The big diameter is 1/2″ (12.7mm), the smaller diameter is 7/16″ (11.11mm) and the thickness of the part is 11/32″ (8.73mm).; so the threaded shaft needs to be longer than that. Let me know if any one has a part number to a round pot that fits it.
Hello,
Here are the kind of potentiometer located in the HS805BB. In the link there is also dimensions.
Potentiometer on Aliexpress
Thank you, I ordered https://www.mouser.com/ProductDetail/652-PDB12-H2251502BF and will post pictures after.
http://inmoov.fr/members/jrenta/album/picture/1880/round_POT.jpg
I can’t find the STL for that “L” bracket for the shoulder’s pivpotholder. Where can I find it.
I have updated that part to hold the bolt at the same time.
http://inmoov.fr/inmoov-stl-3d/?bodyparts=Shoulder&parts=PivPotholderV3.stl
http://inmoov.fr/inmoov-stl-3d/?bodyparts=Shoulder&parts=LeftPivPotholderV3.stl
hello Gael and congratulations for the spectacular project. I have a question to ask, I am assembling the right arm and I do not understand how you can run the cables inside the rotate without the biceps piston cutting the wires. do you have any photos to understand the passage of cables well? thank you
Hello,
You need to make sure to use only flat ribbons other wise it might be too thick in the “RotGear” to let the piston turn freely.
Also you need to use the “RibonPusher” to make sure the ribbons are applied against the wall of “RotGear”.
http://inmoov.fr/wp-content/uploads/2013/09/DSC07386-600×450.jpg
http://inmoov.fr/wp-content/uploads/2013/09/DSC07387-600×450.jpg
https://i.postimg.cc/26mX6jz8/84-E66657-2208-4-ABA-8-C25-8-DFCE8570695.jpg
ok Gael, where does the biceps servo motor cable cross the shoulder? passes externally? from the photos I do not understand. the flat 14-wire cable I have problems after crossing the shoulder with pistonbase, do you have photos to see the finished work? thank you
Hello,
This is the way I do it, the ribon cable slightly turns in Rotgear to come out at the back of the bicep:
http://inmoov.fr/wp-content/uploads/2015/06/image01-e1578044141704.jpeg
http://inmoov.fr/wp-content/uploads/2015/06/IMG_5418-e1578044127257.jpg
many thanks Gael, the photographs are very useful. I see that you also passed the bicep servo motor cable inside your shoulder, right?
I have another problem, the shoulder cannot close inside the torso because the heads of the engine support screws (homoplate) knock in the engine exhaust window
https://i.postimg.cc/fyzTX4Fn/3-CA798-CC-17-FF-4683-BB2-D-2-C2-DA7-F0-CBFE.jpg
https://i.postimg.cc/j2Mq4g0W/9426906-B-436-E-438-B-BFB1-4-AA1-AFC0-FF36.jpg
https://i.postimg.cc/Y2RS79Gp/CECA752-E-B6-CB-4-DC7-BD4-F-B141084-E0019.jpg
Hello,
Normally when the servo hits the exhaust window, it has reached it’s minimum position.
You might want to countersink a little more the screws so that they do not stand out too much.
Hello Gael, could I have a photograph of your shoulder from above to see the passage of the 14-pole cable? Because this is my result but I’m not sure when the cable is rotated it will be cut
Thanks
https://postimg.cc/F1fsf4Mv
https://postimg.cc/gX7zMS61
Hola bueno dias!
Mi nombre es Diego y soy de Argentina! Estoy haciendo la parte del hombro pero quisiera saber si alguien lo modifico para usar un motor paso a paso ya que aca no se consigue ese tipo de servo tan grande.
Desde ya muchas gracias!
Hello,
There has been some people testing step motors in the bicep, but apparently the result wasn’t that great.
Step motors are heavy if you need to obtain 23kg torque, also the power supply needs to be higher which means using another sort of battery.
To see the tests you will need to search on Thingiverse for InMoov derivatives.
I am a noob to Myroborlab and I guess this question has a simple answer but have searched these pages and the web but can not find how to run the “test script” I wish to run InMoov2.minimalArm.py and the other test scripts as the build progresses.
I assume the PY script are ran in MyRobotLab but I do not know were to save the PY file or how to run it.
Any assistance would be greatly appreciated.
Hello,
First I would recommend to use the SERVO_CALIBRATION.bat tool to set your mappings.
See this video for the bicep to understand how to use the tool, it can be applied for all the servo on InMoov.
https://youtu.be/aHVBU02EtxY
Once your mappings are done you can test InMoov directly into MyRobotLab with voice commands with START_INMOOV.bat.
If you want to try using the test scripts anyway:
1-double click the myrobotlab.jar
2-copy paste the python script in the python tab window.
3-run the script by clicking the button “execute”.
Note that the script doesn’t take the mappings from the config files, therefore you need to modify the script manually to set your mappings.
Thank you Gael for your reply and a very big thank you for open source Inmoov.
It is reassuring to know that using Servo_Calibration.bat is the correct process to set up the servos as this is the method I have been using.
Bicep video was a great help with explaining the process.
Hello… How can this work, my shoulder have so small force that he not even can lift his own arm. All things stuck and crunch and nothing fits together. This robot is so frustrating and disillusioning for me, i can not understand how all people can be so fascinated from it, by me nothing works on this robot, i can not build it…
Hello,
It seems the project is maybe too complex for you.
You need patience, determination and a good dose of Do it Yourself.
The printer calibration is something very important to be able to achieve fitting parts.
There is more than 5000 InMoov robots printed in the world and many of them are being used in Universities and schools.
But is this normal, the gear of the shoulder touches a little bit the outer ring when much force is applied? I don’t know if this causes the problem, it is not much, but a little bit friction on the wrong thing and everything can stuck. And also the wormgear is, i think, never absolute centered on the servo, and it wobbles more or less a little bit, what make also a little bit friction, when the lower part is not only held by the servo. And finally, always when i come to a 3d printed wormgear, i only come to the conclusion that a 3d printed wormgear has way too much friction, especially with much force.
The printer should also be good calibrated, a little test cube was at the beginning printed with 0.1-0.15 resolution. And i printed the wormgear with 0.05 layer height, without support, and it is in both directions similar.
Is it true that the inmoov should at the end be able to lift ~ 1.75 kg in the hand? By it’s shoulder motor in horizontal position?
And how long patience do you mean? How long should it take to assembling the complete inmoov (without legs)? I read somewhere a 12 years old boy made it in a month, i’ve been there for several months, and i stuck at every corner by something that not work as expected, and have to reprint or find an alternative. I see it everywhere, the complete eye mechanism is so delicate by me, that i prefer not to use it and be happy when both eyes are looking in the same direction, and if i would, the cameras quickly doesn’t see the full picture, because they are in the eyehole (what is the normal field of vision of a human, but it seems very unhandy to use both cameras for something). And the microsoft cameras doesn’t even fit in the 3d printed place, not only a little bit, i had to remove the half of the tube where a screw comes in, maybe the cameras are produced a little bit different now. And so it goes on over the full inmoov like the shoulder and the eyes, every second thing that moves must be special made and precisely adjusted and fine tuned by hand and maybe reprinted. I can not understand how so many people can build it and even university, and nobody said something about that, or am i the only one who have so many problems with it? Is that the normal build procedure?
Beside this the robot would look fantastic, but the mechanic works absolute not fantastic by me…
A question ?, someone used this Servo Motor Td-8125mg Waterproof Metal 180º High Torque, or similar …? for inmoov, I have a couple of them and although they lift the shoulder blades, I don’t know how to calibrate them, thanks
I ask a question? Someone used this Servo Motor Td-8125mg Waterproof Metal 180º High Torque, or similar …? for inmoov, I have a couple of them and although they lift the shoulder blades, I don’t know how to calibrate them, thanks
Hello everyone! I have completed the shoulder joint! I have to calibrate the servos, I took as a reference the video of the bicep on the InMoov site, but I have difficulty adjusting the potentiometers, as soon as they move by micromilimeters the arm starts !! Can you give me a tip that I’m doing something wrong with a system? They dismember me really too sensitive !! Thank you all
Hello,
Are your Arduino grounded to the main power source?
If not that might be the cause. When the Arduino is not grounded, it creates eratic behaviors when moving the potentiometer.
Hi Gael,
I’ve just mounted the first part of the shoulder, I’m using a different servo and observed than based on your photos on positioning cables for potentiometer it was turning the wrong direction, I then inverted them and it’s ok. But when aligning plastic parts like on your photos to pass cables, that position for my servo using the same round potentiometer than you and positioned in the same way, I’ve an angle corresponding to that position of 150°n not around 30 like yours. Would it cause problem? Is that position corresponding to the Rest one and needed to be 30°? Then when increasing angle, in which direction should it turn from servo view side, clockwise or anti? Thanks
hello I’m building the arm and shoulder and can’t find the stl file for the ThroatHole.
Thanks for responding.
Hello,
This stl is located with the neck.
http://inmoov.fr/inmoov-stl-parts-viewer/?bodyparts=Neck
Thanks, but i have plant too juse a PVC Pipe and connect it too the Trothole Piece. It whut be gread if you cud send me the older version with the circular hole.
Hello, I built the forearm and hand as a school engineering project and used an arduino nano to tell the fingers to contract as part of a bigger project (see https://www.instructables.com/Robotic-Hand-With-Wireless-Glove-Controlled-NRF24L/). I have two questions for the shoulder and bicep. 1. What did you use to power this (power supply)? 2. What mini computer did you use (ex: Arduino uno, etc)?
Hello,
Is PETG filament recommended to build shoulder parts?